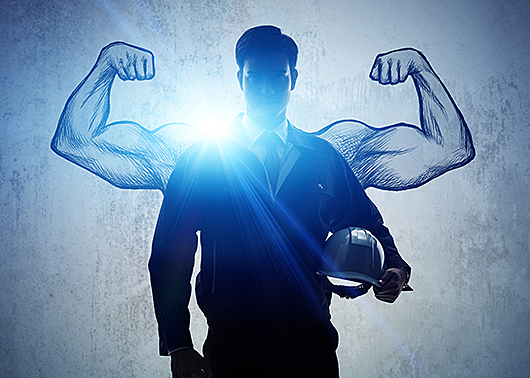
When we think of tough customers, we think of people like Hulk Hogan, Ripley from Aliens, and anyone who works in the construction industry.
Hopefully you don’t have to wrestle or fend off aliens while you’re processing construction materials. For everyday conveying concerns, you need a durable rotary valve to keep production going strong.
It’s all about equipping that valve for durability and longevity. When you have abrasive material like cement, specific features will help your valve resist damage over time — and stand up to the toughest conveying challenges.
Valves: Two solid choices
For this application, it’s best to go with a standard type of valve that can easily be customized with the rotors, coatings, and options you need. At ACS Valves, your choices would be the CI Series valve (a square-flange type) and the MD Series valve (a round-flange type).
Though we have a lot of other rotary valves on offer, you don’t need anything too fancy in this case. These two standard options will be the easiest to configure and maintain.
Rotors: Resisting wear
Construction materials tend to wear down rotor tips more quickly than usual. Your best choice will be a rotor that can withstand all that rough material, so you don’t have to replace it as often. We typically recommend stainless-steel or AR400 steel.
In terms of rotor type, a closed-end rotor provides an extra shield to help protect the outboard bearings and endplates of the valve. It’s recommended for extremely abrasive materials, as well as flake or chip material that is prone to getting stuck in the gaps.
Our rotors are all CNC-machined to precise tolerances. If you want to know more, this video gives a quick overview of why it’s so important to keep rotor tolerances tight.
Coatings: Protecting the housing
When we speak with customers who convey construction materials like cement, we sometimes get questions about replacing the housing of a rotary valve, but this basically means replacing the entire valve. That’s obviously not ideal for you!
That’s why we strongly recommend applying a special coating to your rotary valve. Hard chrome is the most common choice, but heavy plate chrome or tungsten are also good options for even more abrasive applications.
A tough coating will extend the lifespan of your valve and minimize downtime.
Options: Keeping material flowing
When you’re conveying cement and other construction materials, they can sometimes build up around the shaft seal and bearings area of the rotary valve. A shaft seal air purge kit is an optional (but highly recommended) attachment that keeps material away from these sensitive areas.
Cement can also be dense or sticky, so a rotor pocket purge kit can provide additional help with material flow. All this ensures your material moves through smoothly without sticking, jamming, or building up.
Are you tough enough?
Our tips for conveying cement are pretty straightforward, but they’ll help you get the most out of your rotary valve’s lifespan. The right combination of coatings, rotors, and options mean you won’t have to replace it as often.
Want the best rotary valve recommendations for your particular application? We’re here to help. Give us a call to start sizing and configuring your valve.