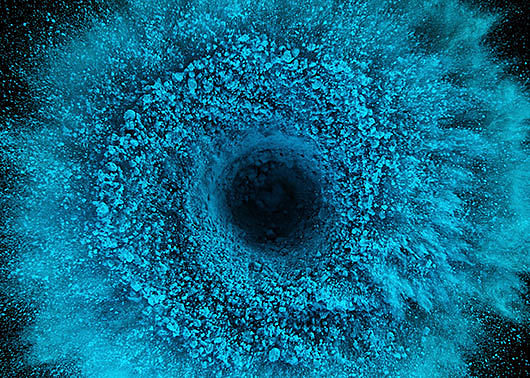
Some things collect dust unintentionally, like that workout gear you got for Christmas or that 400-page novel you’ve been meaning to read. In an industrial setting, some devices are built for collecting dust, capturing lost particles from a material handling system to maintain the air quality in your plant.
To ensure your dust collection system works efficiently, it’s essential to have the right rotary valve. By maintaining a proper pressure differential, the airlock isolates the dust collector hopper from the outside environment while allowing the collected dust to exit the system safely.
Why do I need an airlock?
By isolating dust into a contained stream, airlocks improve the performance of your dust collector system. Rotary airlocks maintain a pressure differential between two separate, differently pressured atmospheres.
Airlocks let you change the dust bin without shutting off your system. Without an airlock, you would need to shut down the system to get rid of dust, and contaminated particles would be free to enter the environment. It’s important to make sure your airlock is properly designed for this purpose.
What makes a good rotary airlock?
With the right design, a rotary airlock should be able to handle high volumes of dust efficiently, which helps improve air quality, keep machinery clean, and keep the environment sanitary.
To prevent the passage of flames or sparks, it’s extremely important to make sure your airlock is NFPA-compliant.
How are NFPA-compliant valves designed?
Rotary airlock design considers how your conveying system should be configured, the type of deflagration protection to use, and the maximum pressure your valve can handle.
Your material characteristics will heavily influence the airlock design, but there are some rules that apply in all cases. All airlocks in dust collector applications must comply with NFPA regulations.
NFPA 69 (Standard on Explosion Prevention Systems) has the details on airlock design, but other key codes include NFPA 68 (Standard on Explosion Protection by Deflagration Venting) and NFPA 652 (Standard on the Fundamentals of Combustible Dust).
Here are some key airlock design rules in plain language (NFPA 69 12.2.4.3.1–12.2.4.3.9):
- The valve housing and rotor must be strong enough to withstand the pressure of a possible explosion.
- The valve design must consider the powder’s explosion characteristics.
- An appropriate testing authority must certify the valve’s pressure resistance.
- The rotor must have 6 vanes at least.
- At least 2 vanes on each side of the housing must have adequate clearances at all times.
- The valve’s body and the rotor vanes must be made of metal.
- The valve must have external (outboard) bearings.
- To automatically stop the valve in case of a deflagration, there must be an independent explosion detection device interlocked.
- Check the laws in your area to determine the need for valve performance testing.
So, which airlock do I need?
We typically recommend the CI Series, MD Series, and SD Series rotary airlocks for dust collector applications. A square flange is the most typical. In most average dust collector systems, airlocks are sized at 10’’ or 12’’.
An outboard bearing design eliminates dust leakage from the endplate shaft seal. For a smooth rotation, the airlock should have a rotor with beveled tips.
If your material is a combustible dust, your airlock should come equipped with an explosion-proof motor.
What optional features should I consider?
You may need high-temperature clearances, a shear protector to prevent material shearing, or a shear pin sprocket in case of jamming. If your dust particles are abrasive, consider an AR rotor, chrome plating, or Tungsten plating to reduce maintenance cycles.
How do I find out about my dust?
Each type of material has different characteristics, and each one in the combustible dust category has a different potential for deflagration.
Annex F of NFPA 68 (2023) has a handy series of tables listing several types of combustible dusts and their deflagration characteristics. The materials are sorted into dust hazard classes. If you’re not sure about your material, you can always have it tested by an independent lab.
What else can I do to protect my workers and plant?
A regular maintenance schedule is essential. Check rotor tolerances often to make sure they stay under 0.0079’’ and replace any part that looks worn. If you haven’t done one already, a Dust Hazard Assessment (DHA) is generally required by NFPA codes and will help you identify any potential hazards in your facility.
OK, where do I start?
ACS Valves designs airlocks with NFPA compliance in mind. To get started, let’s have a conversation about your process and what type of dust you’re handling. Our reps know conveying systems inside and out, and we are always happy to help!