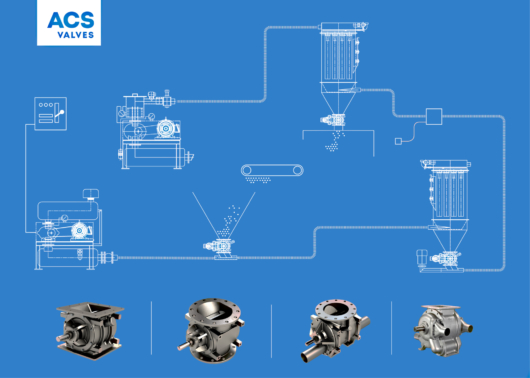
When we say our valves excel in high-pressure situations, we mean it.
As one of the most common and versatile ways to move dry bulk material, pneumatic conveying is the system of choice for all kinds of applications and industries. When it comes to choosing a rotary airlock valve that fits your process, things can get tricky.
How can we convey (pun intended) the value of choosing the right valve? It all comes down to efficiency. The wrong valve could cause problems like premature wear, air leakage, or overall poor performance, all of which slow down production and cost you money.
We always say the perfect choice of valve depends on your material and application. That’s still true, but we don’t want to leave you in the dark. Let's take a look at how specific valves and features can tackle the challenges unique to pneumatic conveying.
Common challenges in pneumatic conveying
Whether you’re using a positive or negative pressure differential — pressure or vacuum conveying — the pneumatic system is all about pressure and air. A pressure system pushes material down the conveying line from the top, while a vacuum system pulls it from the bottom.
Abrasion and wear
Higher pressures move materials faster, and sometimes this makes the material more abrasive than usual. Higher abrasion causes more wear-and-tear on your equipment, forcing you to maintain or replace it more often.
Air leakage
Air leakage is another common issue. In rotary valves, you want rotor pockets to fill with material — that is, an ideal amount that wastes the least amount of time, energy, and product.
With pneumatic conveying, it’s possible to get too much pressurized air in the rotor pockets. This reduces your fill efficiency, and as the rotor completes its rotation, it can also release air back up through the valve’s inlet. That’s not where you want blow-by air to accumulate, because it can cause material flow issues and blockages.
4 valve choices for pneumatic conveying
Your choice of rotary valve should be able to withstand high pressures and have features to protect against leakage and premature wear.
The CI Series and MD Series are kind of like fraternal twins — they’re both drop-through valves with a durable, versatile design, but one has a square flange while the other is round. Their outboard bearing design protects the bearings from high pressures, and they’re customizable to fit almost any application. The standard series handles a maximum of 15 PSIG, while the super-duty series can tackle up to 22 PSIG.
The Aero-Flow and BT Series are blow-through variations with outlets specifically designed to connect to a conveying line. While their designs are distinct, they both excel at handling different types of hard-to-convey materials by reducing air leakage, optimizing bulk density, and maintaining consistent material feed efficiency. They both handle up to 20 PSIG.
Features and accessories
The CI and MD Series valves both need a blow-through adapter to connect to a pneumatic conveying line. To minimize air leakage in high-pressure conveying scenarios, we recommend a rotor with 10 vanes.
For pneumatic conveying systems that exceed 6 PSI and handle pellets, granules, or powders, the most essential valve design feature is a housing vent port. By venting pressurized air through an opening on the side of the housing, the vent port relieves blow-by air before it can interfere with material flow or cause abrasion in your valve parts.
What to avoid
If you have a pressure system, avoid using valves with closed-end rotors. That’s because blow-by air can get into the gap between the rotor shroud (the parts that enclose the rotor vanes) and the valve’s endplates, which eventually causes premature wear to the endplates.
Need help handling the pressure?
If you’re looking for a new pressure or vacuum blower package, we can help with that too. This blog explains more about the differences between the two.
Pneumatic conveying can be a complex topic, but we’re happy discussing anything and everything that has to do with rotary airlock valves. Give us a call to find the perfect configuration for your system.