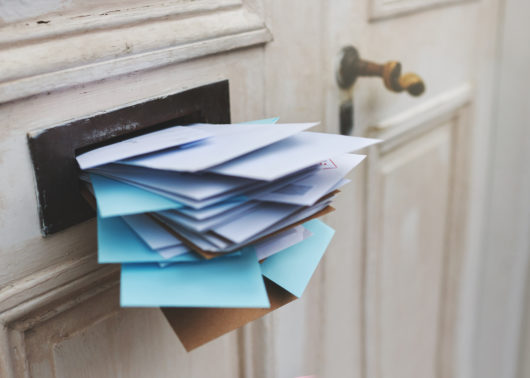
As a manufacturer, you might know the reason chip bags don’t come 100 percent filled to the top. It’s called “slack fill,” and it’s less about cheapness and more about protecting the delicious chips inside, keeping them fresh and undamaged.
Similarly, you don’t fill your morning coffee to the very top because then you’re liable to spill precious caffeine all over your laptop.
You should not size airlocks for 100 percent pocket fill for a combination of those reasons: to protect equipment and material from damage, prevent accidents in your facility, and promote overall efficiency.
Material flow is a big indicator of efficiency. To get the best possible material flow rate, we recommend 70 percent pocket fill for most applications.
You can also improve the flow rate (or feed rate) by accounting for key application details: material bulk density, material characteristics and valve speed. More on that in a moment.
Go with the flow
First, need a visual besides chips and coffee? Here’s a 3D animation of typical material flow and pocket fill in an MD Series rotary airlock valve.
Material Flow in an MD Series Valve
As you can see, a bit of empty space in each pocket keeps the material flowing smoothly. Without that, you could see a multitude of (often inter-related) problems, from jamming to valve wear-and-tear to material leakage.
Now, here are three aspects of your material and application to consider for optimal flow rate, efficiency and productivity.
Tip 1: Material bulk density
As you know, different materials have different bulk density values measured in pounds per cubic foot (PCF). The material’s PCF affects capacity and throughput as it passes through the rotary valve.
For example, the PCF of cement dust ranges between 90 to 60 if aerated. Because an airlock conveys less material at a lower bulk density, the lowest value in this range, 60 PCF, is the one that affects valve sizing.
In other words, make sure you size the rotary valve correctly based on a calculation of the lowest (i.e. the lightest) bulk density value.
Tip 2: Material characteristics and flowability
Some materials just don’t flow as well as others. This could be due to their shape, weight, moisture content, or just a quirk of their composition. These types of products need special considerations.
Lighter products tend to do better with a larger rotary airlock valve. Wood dust, for instance, is very light at 12 PCF on average, and it flows more uniformly through a larger valve inlet. Proper sizing also prevents material buildup on the inlet flange.
To prevent pressurized air from the outlet blocking material from getting to the inlet, make sure your airlock is properly vented to relieve air leakage from the pressure conveying line.
Tip 3: Valve rotation speed
Each valve has an effective maximum speed that varies based on its size. You gain more volume per rotation (and, therefore, a lower RPM) by upsizing your rotary valve — without compromising your estimated material flow rate.
If your materials are abrasive, that’s a good case for upsizing your rotary valve and decreasing your valve speed. This will help to decrease wear on the valve and extend its lifespan. (By the way, you can also mitigate wear with abrasion-resistant coatings and other options).
Need advice? Say no more
Whether you want to improve material flow, throughput, valve longevity or general efficiency, there are plenty of features and options to consider for your rotary valve. Talk to an ACS Valves rep for a breakdown of your best choices. We’ll make it easy to select a valve for your specific application.