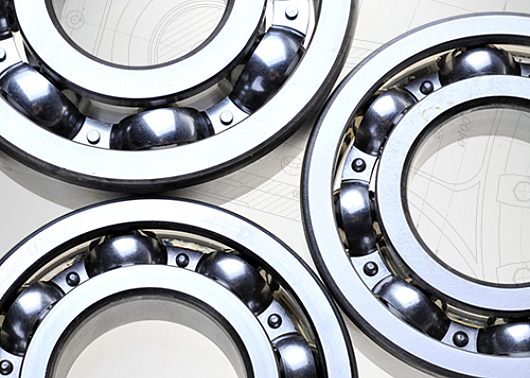
What happens when you throw a wad of $100 bills into your rotary airlock valve? We’ve never tried it, but here’s our best guess: your money gets shredded into pieces that clog up the valve and cause a system failure. Whoops!
Using inboard bearing assemblies is a bit like shredding money. If you have the choice between inboard and outboard bearings, know that outboard bearings will do a better job of protecting your material, your rotary valve, and your facility.
What’s a bearing?
The main component inside your rotary valve’s housing is the rotor, which rotates to help your material move from one container to the next. Bearings support your valve’s rotor and allow it to rotate smoothly.
These bearings can have an inboard or outboard design.
What’s the difference between inboard and outboard bearings?
Inboard bearing assemblies are mounted on the inside of your housing endplates, while outboard bearings sit on the outside of the housing, which means the bearing is separated from the seal by the housing endplate.
When inboard bearings are specified, it’s usually for light-duty applications. Think easy-to-handle materials that are not sticky, dense, or abrasive, as well as conveying setups with a lower pressure differential.
That said, there’s a good case for using outboard bearings even if your material isn’t particularly fussy.
Are outboard bearings better?
Outboard bearings provide an overall longer service life and fewer risks.
Although inboard bearings are specified by some manufacturers to keep costs low, they can lead to more expensive repairs or valve replacements in the event of a seal failure, which poses the risk of contaminating your bearings or wearing them down much faster.
Because outboard bearings leave a gap between the seal and bearings, this risk is significantly lower. If the seal ever fails, material has a path to escape without damaging the bearing components.
In other words, outboard bearings are protected from material contamination or build-up. It costs much less to replace a seal on its own, whereas with inboard bearings, you risk replacing the entire rotary valve and compromising your end product.
How do bearings affect compliance?
If your facility handles combustible dusts, outboard bearings are mandatory for NFPA compliance. Bearings create heat as they rotate and, if they overheat, have the potential to act as an ignition source for dust explosions or deflagrations. Any build-up of material on the bearings could therefore act as a fuel source.
Outboard bearings are located outside of the combustible dust stream, which reduces their exposure to dust, makes them easier to maintain and clean, and makes them more accessible for inspection and monitoring.
Are there any other perks to outboard bearings?
Most of our customers have materials with particular quirks or system requirements, and outboard bearings are much more accommodating in those cases. Their more adaptable design accommodates a higher pressure differential for conveying, alternative shaft seal arrangements, and a wider variety of rotor shaft diameters.
ACS Valves believes in built-in safety features that help our customers save money in the long run, which is why we design all rotary valves with outboard bearings.
Looking for more ways to boost efficiency and safety? Contact us for help customizing a rotary airlock valve that fits your application to a T.