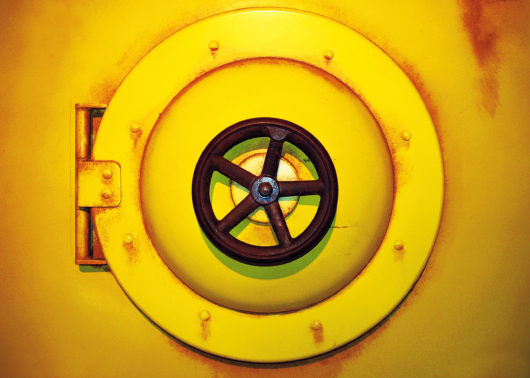
Do you ever wonder what it’s like inside a rotary valve? Is it like a tropical cyclone, whirling helicopter blades or an endless spin cycle in your washer/dryer?
Strangely enough, a valve shares most in common with a cyclone, because both rely on pressure to function. Although, just to be clear, valves are much safer and less destructive.
Rotary airlock valves are designed to maintain a consistent pressure differential. By sealing air flow between the inlet and outlet, an airlock helps maintain ideal pocket fill and keep material flow efficient.
Why do rotary airlocks leak?
Rotary airlocks aren’t 100 percent sealed, and there’s a good reason for that: there must be a small clearance between the rotor blades and housing. A little bit of space lets the rotor, well, rotate, so the valve can operate as normal.
But only a little — if rotor-to-housing clearances rise above 0.0079’’ (something we talk about all the time), it becomes an issue with NFPA compliance. Any gap bigger than that will compromise the valve’s ability to act as an airlock and increase the potential of creating a combustible dust hazard.
To get the best amount of material in each rotor pocket, reduce waste and prevent hazards, clearances must stay below that recommended size. The exact clearances depend on factors such as speed, temperatures and thermal expansion, displacement of the housing under the material load, and rotor runout.
Then there’s something called rotor displacement leakage. When material enters the valve, some air leaks out of those small clearances, while some of it stays sealed inside the rotor as it meets pressure at the outlet. When the trapped air comes around to the inlet, it’s released into the feed hopper and impedes material flow.
Again, this is normal in smaller amounts. Factors such as pressure differential across the valve, rotor pocket volume, product feed rate and valve shaft speed determine the amount of rotor displacement leakage.
Another (unrelated) reason for leaks is worn-out shaft seals. When the shaft seal is too far gone, your material will contaminate the bearing, which will eventually cause the bearing to fail. That means more material leakage and a more expensive repair.
Prevent leaks with these maintenance procedures
Leaks waste material, cause unnecessary downtime and wear down other parts of the rotary valve. It’s important to nip them in the bud!
More often that not, that starts with ordering a valve that is designed for your material and application. ACS Valves has a whole host of accessories, coatings and features that extend the lifespan of your valve and its many moving parts. A few examples include coatings that resist chemical corrosion, rotors that work better with abrasive material, and materials that prevent build-up of fine, sticky powders.
That just means your valve is equipped to last longer (and cost you less to operate) from the start. From there, you should know the right maintenance procedures to diagnose, prevent or repair leaks.
One is to check your rotor-to-housing tolerances every three months, and then replace the rotor if the blades have worn down too much. You should also keep spare shaft seals and packing on hand — we recommend a four-lobed seal.
Oh, and another general tip: always go with OEM parts. Some look for replacement parts elsewhere, and they often end up being sized incorrectly. ACS uses precise measurements and drawings to make sure your spare parts always fit.
The future is not so (b)leak
If you keep up with regular maintenance and check parts for wear, you should be able to steer clear of leaks. The ACS Valves team is here for you if you have any other questions.