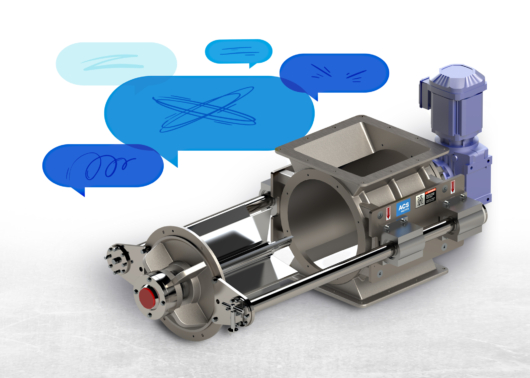
We all have ways of letting the world know we need attention, whether it’s posting a picture of your dessert on Instagram or flopping over to show your belly (this one mostly applies to dogs and cats). Rotary airlock valves also have a way of showing they need some love — or repairs and maintenance.
If you notice any signs your valve needs attention, take a look as soon as possible. Because everything is connected, the issue can snowball if one damaged part starts wearing down other areas of the valve.
We’ll share some general tips to help you diagnose the issue. One last note before you start: always remember to lockout and tag your system before handling the machinery.
Sign 1: You hear weird noises
Your valve may not bark or meow to let you know it’s hungry, but if there’s a problem, it might make strange noises or sound much louder than usual.
One possible cause is that the rotor is moving in the wrong direction. Check the markings on your valve to confirm the right direction and, if necessary, rewire the motor to correct the issue.
Valves can also make noise when too much material builds up in the rotor clearances, or when a foreign object gets jammed inside. Open up the valve and clean any buildup you find. The clearances can also change due to thermal expansion, so check the manual for instructions on how to measure and adjust them.
Another cause of noise is the drive chain or drive shaft rubbing against the guard. In those cases, you should be able to solve the problem by adjusting the guard, the sprocket position, or both.
If none of those apply, you might have a failed bearing. Remove and inspect the bearings and replace them as necessary.
Sign 2: The rotor won’t rotate
A valve with no rotation is like an ice cream truck with no ice cream — what’s the point? The worst-case scenario here is a broken shaft, because the only solution is to order a new valve.
Thankfully, there are a handful of other causes you can investigate first. Check the motor and its settings to make sure you’re getting power to the airlock. It’s also possible that a foreign object is stuck in the inlet throat, in which case you can simply inspect that area and remove the blockage.
No luck? If your setup has a drive chain, you can inspect that for signs of wear and replace it as needed. The same goes for your gearbox — take a look and replace it if you see any damage.
Sign 3: Your seals wear down quickly
Did your shaft seal wear down faster than usual? It could be as simple as adjusting the position of the seal to make sure it’s properly fitted to the valve. Alternatively, you might have the wrong air purge pressure. Check the valve instruction manual to adjust it to the correct pressure for your situation.
Sign 4: Material isn’t flowing smoothly
From bridging to ratholes, you can see all kinds of material flow issues in a conveying line, and they aren’t always related to the airlock.
Start by checking the supply source upstream of the valve to make sure it’s operational and receiving material as expected. The conveying line’s piping layout or size, as well as increases in pressure, can cause material flow issues, so it’s worth reviewing all of those.
On the valve side, you may need to adjust the motor speed or replace sprockets to prevent the rotor from turning too fast. The cause could also be too much rotor pocket fill — an accessory called an inlet shear protector can help there — or excessive blowby air, which means too much air is passing through the valve. That’s usually due to a change in rotor clearances, but vents or vented shear protectors can also help.
Finally, materials with too much moisture are prone to causing flow issues. Problems at various points in the conveying line could contribute to excess moisture, but on the valve side, you should start by cleaning the rotor and checking the flange connections to make sure they’re properly sealed.
Sign 5: Material is leaking
No one likes wasting product, but leaking material can also be a source of combustible dust that increases the risk of fire in your facility and should be addressed as soon as possible.
Leaks are a common sign of worn shaft seals, so it might simply be a matter of replacing a seal. It’s worth checking your rotor-to-housing clearances too, because when they expand too much, the increased air flow can compromise the seal, reduce the valve’s capacity, and increase pressure in the shaft seal area.
Still stuck?
If none of these are working or you need more information, feel free to contact the friendly conveying experts at ACS Valves. We can tell you more about the best ways to prevent these issues in the first place, how to extend the maintenance cycles of your rotary valves, and even how to troubleshoot other areas of your conveying setup.
Just ask — we’re happy to help!