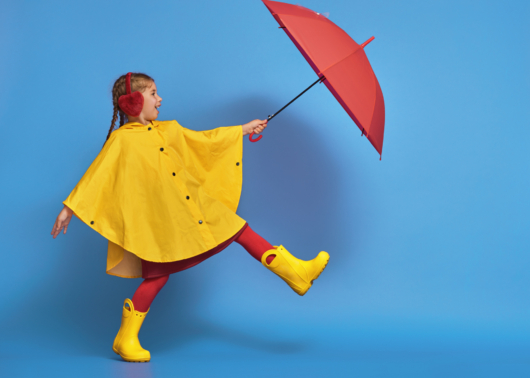
Raincoats are good for singing in the rain, trench coats make you look like a detective, and XTR-Coats make your cast valve FDA and USDA compliant.
No, that last one is not for humans. If your application involves processing corrosive or sticky material, the new XTR-Coat coating protects your rotary airlock valve and extends its lifespan.
Then there’s stainless steel, chrome, tungsten and Lectrofluor. Your choice of coating has a huge impact on the performance of your rotary valve and affects how often you maintain, repair and replace it. In other words, the right coating saves you time and money.
What if I don’t want a coating?
Everyone knows a guy who wears shorts in the winter. Don’t be that person.
Or, if you are that person, just imagine what it would be like to always have warm legs and less downtime dealing with various issues in your conveying line.
Are you with us so far? Here’s what you need to know about coatings.
Two ways to coat
Most often, you want to coat a rotary valve for one of two reasons: to reduce material build-up and improve cleanability, or to reduce wear and abrasion. Sometimes it’s a bit of both.
The first scenario tends to happen with fine, sticky materials such as flour and sugar. Those build up inside the valve over time, which disrupts the rate of material flow and prevents you from getting the most efficient pocket fill. If build-up isn’t dealt with soon enough, it can cause quality issues or contamination.
Otherwise, you’re looking at issues with corrosion or abrasion. A heavy-duty application or one with corrosive materials, whether it’s gravel or cement, can damage the valve’s internals and wear down the rotor prematurely.
Both issues can create a sandblasting effect that wears down your rotor-to-housing tolerances, which means leaking material, reduced efficiency and a possible loss of NFPA compliance.
Some coatings, like the XTR-Coat, can minimize both sticking and abrasion. It also resists temperatures up to 550° F. That said, the best choice of coating for your process will always depend on your material, application and equipment.
Coatings for every material type
Coatings can be applied to your valve’s housing, endplates and rotors. Here’s a quick guide to help you choose based on the material.
Lighter, not too sticky (Powdered sugar)
At the lightest weight and abrasion level, you don’t see as much sticking. The best choice for this is a hard chrome coating for the housing and endplates, plus a Lectrofluor coating for the rotor. That gives you the best abrasion and sticking resistance for this category, along with FDA and USDA compliance.
Light and sticky (Flour and granulated sugar)
The main differences between this and the previous category are weight and moisture. Here we’d recommend a 304 stainless steel rotor with the rest coated in XTR-Coat, because it’s easier for heavy, sticky materials to slide off and prevent buildup in the rotor pockets. It works well as an affordable, food-grade alternative to hard chrome — and it also complies with FDA and USDA regulations.
The stickiest materials will harden at the slightest hint of moisture, causing more serious buildup. In these instances, consider investing in an entire stainless-steel valve, preferably on rails to make cleaning easy.
Moderately abrasive (Cement)
The next level of abrasiveness requires a hard chrome or a thicker heavy plate chrome coating, which goes on the housing and endplates. A stainless-steel rotor can be easily replaced as needed.
Corrosive (Salt)
XTR-Coat is also designed to convey corrosive, acidic or abrasive materials, although it works in a wide range of scenarios. It’s super durable and works double-time as an FDA and USDA-compliant non-stick surface that combines well with a stainless-steel rotor to convey flour, sugar, pet food, salt and more.
Highly Abrasive (Silica Sand)
The most rugged materials call for Tungsten, a type of metal famed for its toughness and high melting point. The tungsten coating can be applied to everything you need — housing, endplates and rotor — to give your valve that protective armor against abrasion.
Wait, I still don’t know what to pick!
No problem! There are plenty of good choices, and ACS is here to help. Our conveying experts can evaluate your material, machinery and overall process to recommend the best coating for your needs.
Give us a call to get started.