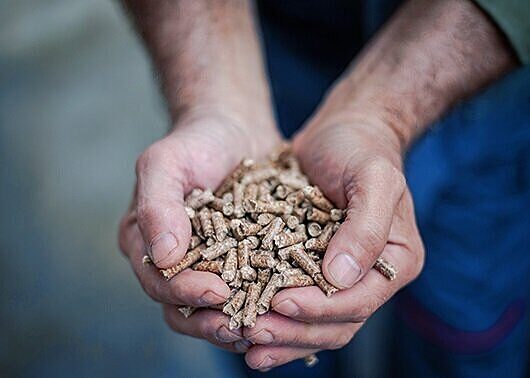
Most New Year’s resolutions are destined to be broken, but rotary airlock valves should be designed to last. Shear pin sprockets are a key part of extending the valve’s lifespan, preventing downtime, and saving you a ton of extra work so you can focus on training for that marathon or finally writing that novel.
Located on the rotor and motor shafts on valves with drive chain packages, sprockets help the rotor spin reliably. That’s how your bulk material gets conveyed. Shear pin sprockets are basically an upgraded version, fitted with a central hub and a tiny cylinder called a shear pin.
That little shear pin is your rotary valve’s strongest line of defense against damage to its more vital components, like the motor and rotor shaft.
When material jams inside the valve, shear pins are designed to break first, preventing more significant failures and saving you a lot of time, money, and stress.
Want a visual demonstration? Check out the video here.
Where do sprockets go in valves?
There are all kinds of different sprockets used in manufacturing applications, so you’re probably familiar with the concept. Just in case: they’re basically wheels with teeth that fit into the grooves on a chain or belt.
Valves with a gear motor have one small sprocket and one larger sprocket. The small one is driven by the motor. As it rotates, its teeth move the chain to rotate a larger sprocket attached to the rotor. As the rotor spins, the valve conveys material.
What can go wrong inside the valve?
When you’re conveying tricky materials like sawdust, woodchips, and plastic flake, flow issues can create a jam inside the rotary valve.
When that happens, the rotor slows down and stops, which makes the large sprocket stop rotating as well. Because the small sprocket is still turning by virtue of the motor, it pulls the chain, which then applies stress to both sprockets, the motor and rotor shafts, and the chain itself.
When a rotor shaft bends even slightly from that strain, the whole rotor is rendered unusable.
How do shear pin sprockets work?
Unlike regular sprockets, shear pin sprockets come with a shear pin nestled inside a hub in its center. A shear pin is a tiny cylinder with an even tinier middle. This small-scale design element is the key to protecting the valve from significant damage.
The small diameter of the pin’s waist is calculated based on load conditions. When the valve jams, the pin shears or breaks, and the hub will stop moving as the large sprocket continues to spin.
This prevents the critical components from getting strained and keeps the chain, motor, sprockets, and rotor in working order.
What should you do after the shear pin breaks?
If you have a Zero Speed Switch Kit installed, you’ll get a signal to indicate that the rotor shaft has stopped rotating. Do your lockout and tag procedures before touching any components.
Then all you have to do is clear up the material jam inside the valve and replace the broken shear pin with a new one. Pins come in packs of ten, so we recommend keeping at least one spare pack on the shelf, just in case.
Does your valve need shear pin sprockets?
If your rotary valve has a direct drive motor, you don’t need to worry about shear pin sprockets — direct drives are streamlined down to a few key parts.
If it’s a chain drive assembly, your local rotary valve expert can determine whether shear pin sprockets are beneficial for your application. We’ll recommend them if we think it will save you more time and money down the road.
So, have any questions, comments, or New Year’s resolutions to share? Need help with material jams and flow issues? ACS Valves is here to help, so give us a call today.