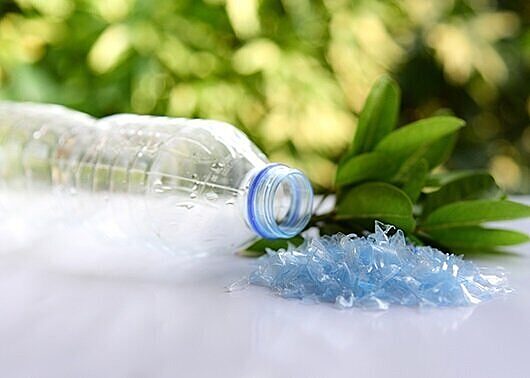
Recycled plastic flakes sound innocent until you try to pronounce their chemical name: recycled polyethylene terephthalate (rPET for short).
In their next life, plastic flakes can turn into all kinds of useful things: bottles, takeout boxes, clothing, carpets, automotive parts, you name it.
But the journey from flakes to t-shirt fibers can get a little bumpy. Because they’re so delicate, recycled plastic flakes are prone to melting together and forming large, irregular shapes that get stuck in your conveying equipment.
If you’re in a food grade or sanitary application like bottle-to-bottle recycling, you’ll also be keeping a close eye on product purity. These tips will help you maintain the best material throughput with minimal damage, waste, and contamination.
What can go wrong?
Plastic processors often need sophisticated equipment just to sort and filter rPET flake material, not to mention convey them from one step to the next. Melted clumps of plastic flake can lead to unwanted downtime and damage your equipment.
In rotary airlock valves, that could look like a significant material jam in the rotor-to-housing clearances. When that happens, the valve can jump, which can then damage the rotor shaft to the point that it needs to be replaced.
Improving material flow
In general, recycled plastic flakes have very different properties compared to other plastic materials. Their relatively low bulk density, coupled with irregular shapes, make it necessary to control material flow carefully.
We recommend the standard rotor speed of 15–20 RPM for recycled plastic flakes. Running it faster could cause bridging above the rotary valve or material jams in the clearances, while running it slower runs the risk of overfilling your pockets with material.
The standard speed provides 70 percent pocket fill and keeps material moving at maximum efficiency.
Make sure the rest of your system is set up specifically for flakes, because the same equipment and configurations might not work for materials like pellets or chips.
Configuring valves for plastic flakes
Closed end rotors keep plastic flakes away from the valve’s outboard bearings and prevent material buildup and jams. Air purge kits support material flow by blowing escaped flakes away from shaft seals and bearings, sending them back to the rotor pockets for a continuous flow.
Shear protectors are another key accessory. Their design prevents material from jamming in the rotor clearances and damaging the rotor shaft.
For plastic flakes, we recommend the standard CI Series valve or the S-Pellet Series, which comes equipped with a shear protector.
Extending equipment lifespan
Your conveying equipment should be properly set up to resist abrasion from the recycled plastic flakes. In most cases, rotary valves made from cast iron are a strong choice.
If you’re in a sanitary application or you’re conveying wet flakes through the valve, you’ll need a stainless-steel valve with sanitary coatings on the rotor and housing.
If you’re still concerned about longevity, remember: maintenance is your friend. Check rotor-to-housing clearances as part of your regular maintenance schedule, and replace rotors as needed. This will reduce the risk of issues like material leakage, damage to other parts of the valve, and bridging above the inlet.
Find the right fit
Like most types of conveying equipment, rotary airlock valves are not interchangeable. Make sure it’s sized and configured to your specific application by contacting an ACS Valves expert in your area.