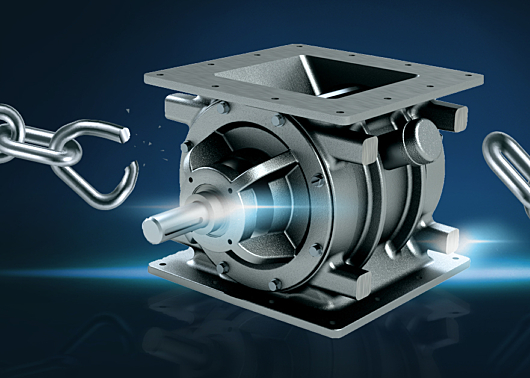
The oldest known chain drive dates back to the 3rd century BC in ancient Greece. It was used to build a polybolos, a repeat-fire ballista that shot arrow-like rods using a flat-link chain drive system.
Chain drives have come a long way since then, and they’re certainly used for more peaceful purposes these days, rotary valve motors among them. But there is a more modern alternative: one that operates with fewer moving parts, making it safer and more efficient.
ACS Valves designs and manufactures two types of valve drives: the more traditional drive chain package and the new-and-improved direct drive. Because of their cost, safety and time-saving benefits, we think more of our customers would benefit from direct drive valves.
What’s the difference, and why do direct drives have the competitive edge? Here’s a breakdown.
The old ball-and-chain
The chain drive on your valve is side mounted to the rotor with a chain, sprocket and mounts. Direct drives are mounted directly on the rotor shaft, which eliminates all those extra components.
Direct drives work well in any application, but they are particularly useful with dust collection systems. It’s always important to ensure they are sized properly for your application, whether it’s light or heavy duty.
Because direct drives have fewer moving parts compared to the chain drive, they come with a whole host of added benefits.
Broken chains are a pain
With all those extra components, chain drives create more potential for something to go wrong. Chains can break or stretch, requiring unplanned repairs or maintenance that increase downtime, including regular inspections to check the chain’s tension and lubrication. If you’re working in a sanitary application such as food manufacturing, lubrication increases the risk of contamination, which means more cleaning to mitigate the risk of product recalls.
Direct drives are easier to install, have fewer parts to maintain and have a longer lifespan overall. All that translates to better productivity in your plant.
Fewer parts, less risk of injury
By virtue of having fewer parts prone to failure, direct drives are also safer. Less maintenance and fewer components reducing your workers’ risk of injury from various hazards. Unlike chain drives, they don’t have exposed rotating shafts — potential pinch points — on either side of the valve.
Because direct drives are mounted on the rotor shaft, they can give feedback to a sensor on another part of the rotor, which adds precision to your system and further reduces pinch points and hazards.
Bonus points for direct drives
Direct drive packages make it easier to change the speed of rotation on your valve. The motor can be equipped with a variable speed drive or variable frequency drive (VSD/VFD), which lets you increase or decrease the speed by turning a dial. As a result, you waste less power in higher rotations per minute (rpm) and get less friction in the chain assembly.
Both types of motors typically have reduction gearboxes, but direct drives don’t have to deal with chain friction. They save power as a result, pumping out higher torque at a lower rpm.
Lastly, chain drives have more parts that will vibrate, which makes them a bit noisy. Direct drives are more compact and quieter to operate.
See the difference with direct drives
ACS Valves still manufactures chain drive packages, of course, and we’re always happy to recommend features to optimize your rotary valve’s safety and efficiency. That said, we believe direct drives can boost manufacturing efficiency in a wide variety of applications.
Want to find out how a direct drive will improve your operations? Get in touch with a representative for more tailored advice.