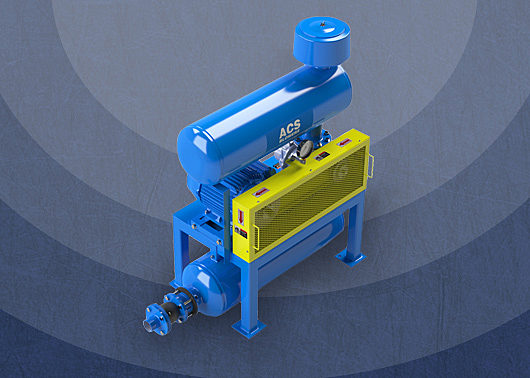
The toe bone’s connected to the foot bone, the pressure blower’s connected to the rotary valve, and the vacuum blower’s connected to the vacuum filter — just not all in the same conveying system.
Toe bones aside, if you’re looking to replace parts in your pneumatic conveying line or install a new system altogether, you’ll need to know the difference between pressure blower and vacuum blower packages. Materials need to get from one end of your line to the other, after all, and they’ll need the right kind of blower to get there safely and efficiently.
ACS Valves offers pressure and vacuum blower packages for dilute-phase pneumatic conveying systems, but what do these packages actually entail? How do you choose the right package for your operation?
Let’s take a look at the basics.
Push and pull: Two key differences
When it comes to pressure and vacuum blowers, two main factors differentiate the systems: the function of the blower, and the location of the blower on your conveying line.
Pressure blowers sit at the start of your line and push materials through to the end. The blower is connected to the conveying pipeline along with a back-check valve, which prevents material from entering the blower, and a flex spool to reduce vibration.
In these cases, the conveying line is generally meter fed by a rotary airlock valve at the material input point, where air and material mix in what could be described as a mini-hurricane. The pressure blower typically pushes the material to the end of the conveying line through a filter receiver.
Pressure blowers come with spring-type mechanical relief valves for over-pressure situations like line plugs. They’re most commonly used for silo unloading, material bin unloading, and similar applications.
On the flipside, vacuum blowers are located at the end of the conveying line, using suction to pull material through the pipeline from the material feed point. It’s possible to pull the material through multiple pickup points to a single destination.
Rotary airlocks or vacuum take-off boxes with air control are generally used to control the material feed into the line, sometimes accompanied by mechanical relief for over-vacuum situations, which can also include line plugs.
Choosing the right blower package
How do you know which blower package is right for your operation? You’ll have to consider a range of factors like the length of your conveying line, the materials you’re conveying, and the density of your materials.
When you have a longer conveying line, we will almost always recommend a pressure blower. They’re ideal for moving heavier materials over longer distances. You can use pressure blowers for abrasive or dense materials, like cement and limestone, as well as dry nonabrasive materials with a light bulk density, like sugar and flour.
Vacuum blowers are less commonly used, but they excel in specific situations. They’re better for free-flowing, non-abrasive materials like flour, wood shavings and fibers. Vacuum blowers also come in handy when you’re conveying pressure-sensitive materials like wheat and grain, which can get damaged or compacted together in a typical pressure system.
What’s in a blower package?
So what actually comes packaged in with your blower package? It depends on your needs. ACS Valves will typically look at your specs — including the conveying line size and length, the material being conveyed (and its bulk density), and the number of long radius elbow piping bends — to build a blower package that works well with your system.
The blower may be paired with a rotary valve, which feeds the material in at a uniform rate to keep the line from plugging up. You may also need components like a blow-through adaptor, a stand, a motor, a pressure relief valve, a belt drive, and an inlet and outlet silencer to keep the whole process at a minimum sound level. Sound enclosures are available as an optional add-on for additional noise reduction.
Don’t blow off your maintenance schedule
Once you’re hooked up with the right blower package, you’ll need to make sure it’s properly maintained. Blower maintenance generally involves checking the oil levels inside the blower to make sure the lobes or gears run smoothly. You’ll also need to check on the belt drives periodically to make sure they’re intact and taut and replace or tighten them as needed. Safety checks should be performed on a weekly to monthly basis.
Now that you’ve had a crash course on pressure and vacuum blowers, you might want to make sure your valves are up to scratch. Contact an ACS representative to find out if you’re using the toughest, most accurate, or most efficient valve for the job.