Your rotary valve accessory guide

Some accessories make you look fashionable. Others help your rotary airlock valves work safely, smoothly and efficiently.
Would rotary valve accessories impress your friends at a fancy dinner party? Hey, you never know — but the important thing is that they benefit your conveying process in various ways. Here’s an overview of the options we provide at ACS.
For jam prevention: Shear Protectors
Granular materials such as plastic pellets, plastic flakes, wood pellets, and other large or bulky materials are prone to rotor jamming. That’s where different types of shear protectors come in. As material enters the valve’s inlet port and fills the rotor pockets, the shear protector’s wiper blade sweeps any overflow into the next pocket. This stops materials from getting stuck in the clearances between the rotor and housing.
Shear protectors come in different shapes and styles to fit your conveying line: there’s a standard spool style, a vented spool style that releases pressured air, and a half-moon style for systems with height restrictions. All three come in square or round options.
For wood dust: Inlet Shunt with Tip Cleaner
Similar to a shear protector, this one is highly recommended if you’re conveying wood dust. The inlet shunt’s shape restricts the valve inlet slightly, and its rubber tip cleaner wipes the rotor tips as they spin, helping to prevent material jamming.
For safety: Discharge Finger Guard
Keep those fingers safe! With options for round and square inlets, this mandatory safety feature protects workers from rotary valves with an open or exposed discharge area. It’s fully CSA and OSHA compliant.
For connectivity: Discharge Blow-Through Adapter
A discharge blow-through adapter connects the discharge of your rotary valve to a pressure conveying system. In other words, it takes material from the valve’s outlet port and blows it wherever it needs to go in your plant. We often recommend pairing this with a vent box, as you’ll see below.
For air release: Vent Box
A useful option for pneumatic conveying lines, the vent box usually sits above the valve. As pressurized air comes up from the line, it leaks into the empty rotor pockets on their way back up the valve. The vent box relieves this air to keep your process going smoothly.
For gravity flow: Maintenance Slide Gate
With different settings to help you control the flow of material, the maintenance slide gate is designed for gravity-flow applications. The air-operated version comes with variable slide gate actuation so you can keep it partially open, fully open or fully closed. It also comes with options for electric slide gate actuation, pneumatic operation or manual operation.
Bonus: Kits for material aeration, safety and speed monitoring
That sums up the main accessories, but there are so many more options to outfit your valves that we can’t fit them all in one blog. You could also consider kits: there’s one to monitor shaft speed, one to cover exposed areas of the shaft, and a few that blow compressed air into areas of the valve that may be prone to material buildup. Feel free to ask us about them!
Which accessories are right for your valve?
By now, you’ve probably realized that your choice of accessories depends on your application. The right ones help to keep workers safe, extend maintenance cycles and boost conveying efficiency. ACS Valves is here to help with that decision: when you work with us, we can recommend the best accessories to complement your process. Give us a call to get started.
Categories: Conveying Systems , Reliability
Go ahead, make your valve
Put your own spin on our customizable valves to get the best valve for your application, material and industry.

We have a series of items available for quick shipment
Items include: Pressure blower packages, MD Series, S-Pellet Series, Diverter Valves, Flex Tip Series, Screw Conveyors
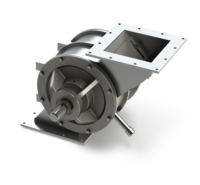
How to: Check rotor-to-housing tolerances
Keep your rotary airlock valve compliant with NFPA guidelines and maintain strong performance by checking your rotor-to-housing clearances regularly.
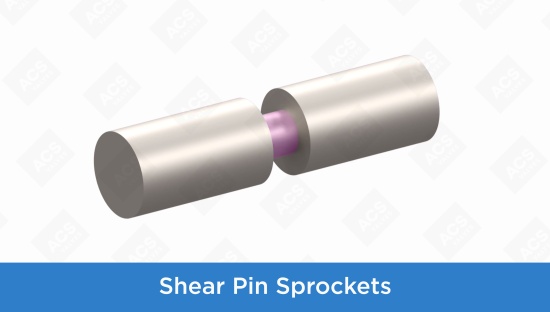
Newsletter
Stay informed on all things ACSWe’ll keep you up-to-date on the latest valve how-tos, handy tips, and news from ACS. It’s totally free and you can opt out at any time.