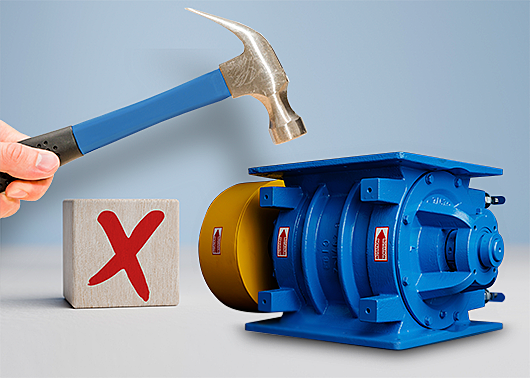
Every once in a while, we hear stories about valves that were hit with tools or left outside in the cold. After all the care we put into designing and manufacturing rotary airlock valves, we must admit it brings a little chrome tear to our eyes.
But that’s not the main reason you should treat your valve with care. As something that joins all the moving parts of your system, a rotary valve is an investment in your material, your conveying line, and even your workers. Mistreating your valve means putting all those investments at risk.
To keep your plant safe and efficient, we kindly ask you not to do the following things to your valve. Hear us out — you’ll be glad you did.
1) Don’t hit your valve with tools
A valve doesn’t feel pain, but it does have parts designed for precision and protection. Hitting the valve with a hammer or screwdriver might seem like a good idea if you have issues with material flow or buildup, but it can cause bigger problems in the long run and reduce the lifespan of your valve.
If you’re experiencing problems like material blockage, slow performance, or strange noises, you may need to do some maintenance or replace a worn-out part. Check out our troubleshooting guide or give us a call — we can help you diagnose the valve’s issue or recommend features that may be better suited to your application.
Oh, another note: don’t use a pipe wrench on the drive shaft. Here’s why.
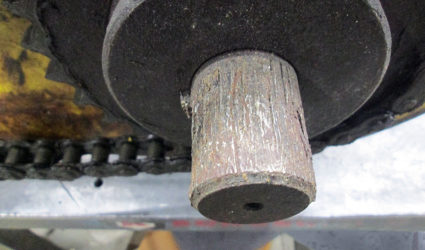
2) Don’t install your valve backwards
This one may seem obvious, but we do see valves set up incorrectly from time to time. This can lead to issues with the valve’s operation and interfere with the flow of material between the valve and any bins, hoppers, or other equipment above and below it. Or it just won’t work. Check your installation guide to make sure the valve is set up in the correct orientation.
3) Don’t leave your valve outdoors
If you order your valve in advance and don’t need to install it right away, it should be stored indoors in an enclosed, temperature-controlled facility until you’re ready to use it. Weather conditions like cold and rain can cause the machined surfaces to accumulate condensation, which can then lead to corrosion or possible safety hazards.
Is your valve outside already? We recommend using a hand truck, forklift, or overhead crane with slings to move it into a clean, dry location. Keep the weatherproof covering on with only the vented parts exposed. Make sure any condensation has time to dry before you apply power to the unit.
For more details, check your valve’s handling and storage instructions.
4) Don’t overstuff your valve
We understand the need to speed up production, but when you stuff your valve with too much material, the opposite happens. Overstuffed valves can cause material buildup, blockages, and damage to your material and equipment. This video demonstrates why.
For most applications, 70 percent pocket fill is the ideal number to keep your valve performing efficiently. You can improve the flow or feed rate with a bit of math around your material bulk density, material characteristics, and valve speed — something else we can help with.
5) Don’t touch a moving valve
Locking out and tagging equipment is an absolute must for worker safety. Make sure everyone is trained to fully power down the valve and perform lockout procedures before doing any maintenance, repairs, or inspections on the valve. The key places to watch out for are shear points and pinch points, such as exposed shafts or areas where the rotor and housing meet. In other words, keep your fingers clear.
When in doubt, call ACS Valves
If you’re not sure about something, get in touch with the experts at ACS Valves. We can help with anything from replacing a set of instructions to troubleshooting an issue with your rotary airlock valve. And if you did one of the things we said not to, don’t worry — you’ll get no judgement here.