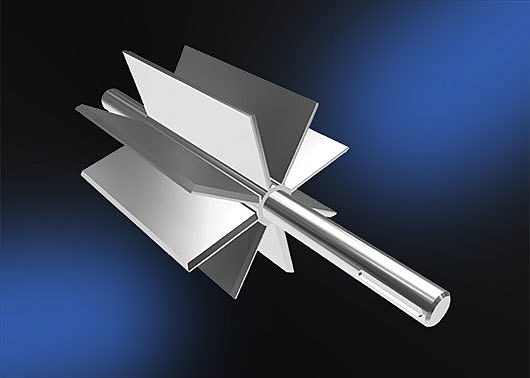
They say life is like a box of chocolates, but what if your choice of chocolate impacted your day-to-day life? Would a piece of salted caramel slow you down? Would a raspberry-filled sweet make you work faster?
Unlike chocolates, you need to choose rotors carefully. They affect your rotary airlock valve’s lifespan, its maintenance cycles, and its ability to convey dry bulk materials efficiently.
This guide will help you choose the right rotor depending on your material and application.
To get started, here’s some quick rotor terminology:
- Vanes: The rotor pockets that contain the material as it passes through.
- Blades: The parts that stick out from the rotor shaft. Two rotor blades form a vane.
- Shaft: The rotating bar that turns the whole rotor 360 degrees.
- Tips: The outer edges of the rotor blades.
Overall: For NFPA Compliance
If your material produces combustible dusts as outlined in the NFPA guidelines, you’ll want to start by taking note of a few things. To stay compliant, rotor blades should be 3/8’’ thick, and the tips should be made of steel. That means you’ll want to avoid any options that come with rubber tips.
You also need to make sure two or more rotor vanes are always in contact with the housing as the rotor spins. These rotors should have 8, 10, or 12 vanes.
Once you have the right rotor, you’ll need to keep a regular maintenance schedule to ensure your rotor-to-housing tolerances stay under 0.0079’’ — and ideally replace the rotor before tolerances grow too large.
Standard Configuration
Open End Rotor
Industries: Chemical, Food, Pet Food, Pharmaceutical
This is the popular kid in school: the standard rotor design with V-shaped vanes. It’s an all-around solid choice because it’s NFPA compliant and easy to maintain. It’s well-suited to a wide range of materials and applications.
Sanitary or Food-Grade
Radius Pocket Rotor
Industries: Food, Pet Food, Pharmaceutical
The Radius Pocket Rotor is like the cousin of the Open End Rotor, but with one key difference: the vanes are U-shaped instead of V-shaped. The smooth U minimizes material packing in the crease of the rotor vane, which simplifies cleaning and makes it much better suited to sanitary or food-grade applications.
Bolt-on Serrated Tips Rotor
Industries: Chemical, Food
The name says it all: this rotor has one or two serrated tips secured by bolts that are adjusted to a smaller clearance. Why? When you have granulated or sticky materials, those jagged edges scrape the inside of the valve to remove any build-up that accumulates on the surface. That means less maintenance for you and a smoother flow overall.
Abrasive Material
Closed End Rotor
Industries: Chemical, Construction, Plastics
With this rotor design, a disc attached to both sides of the rotor blades prevents the blades from touching the endplates. It’s machined precisely so that if any material ends up outside the rotor, it can easily fall out through the bottom of a gap between the disc and endplates.
The discs are like a shield for the endplates and outboard bearings, protecting them from damage and material buildup. Consider the Closed End Rotor if you have extremely abrasive material, flake, or chips.
Adjustable Rotor
Industry: Construction
Moderately abrasive material can wear down rotor tips prematurely. In these cases, we might recommend a rotor with adjustable tips. Rather than replacing the entire thing, you can renew the clearances on this type of rotor by only replacing the blades. It’s a faster and more economical way to keep your rotary valve compliant. Find a how-to guide for this process here.
Fibrous or Flaky Material
Flex Tip Style Rotor
Industry: Plastics
Fibrous materials, flakes, and chips are more prone to jamming in your system, but you may not want features that will slice up the materials or damage their shape. That’s where rotors with flexible tips come in handy. As the material passes through, the tips can bend out of the way to let everything flow while keeping a tight seal.
Adjustable Polyurethane Tip Rotor
Industry: Plastics
Another version of the Flex Tip Style Rotor, this one is better suited to plastic pellets, regrind, and flakes. It combines the adjustable design with flexible polyurethane tips to prevent material jams and maintain a proper seal inside the valve.
Uniform Material Flow
Helical Rotor
Industries: Chemical, Food, Pharmaceutical
As the Helical Rotor rotates, its slanted design cuts through stubborn material. If the material is about to get stuck between the rotor and housing, the rotor blades will act like a knife, slicing up the material and continuing to move. This rotor is commonly used for conveying wood chips, but it’s available in an open or closed end design for different applications.
Staggered Pocket Rotor
Industries: Construction, Pet Food, Pharmaceuticals, Plastics
When constant or pulse-free flow is critical, this rotor brings a set of 16 offset vanes to maintain a continuous flow of material.
As material moves through a regular rotor, there are pulses as the rotor vanes pass from inlet to outlet. The staggered-pocket design offsets these pulses for smooth, constant movement of material through the system.
Metering or Small Batches
Metering Rotor
Industries: Chemical, Food, Pharmaceutical
These rotors are all about precision. If you’re running test batches or smaller amounts of powdery material in an extremely controlled flow, the Metering Rotor’s tiny grooves help to maintain the accuracy you need.
Reduced Volume Rotor
Industries: Chemical, Construction, Food, Pet Food, Pharmaceutical
In another metering scenario, sometimes you need to reduce the cubic foot per revolution (CFR) of the rotary valve. If there is too much material moving through a system or it flows through too easily, it could clog up the line downstream of the valve. The Reduced Volume Rotor makes it easier to control the flow by reducing CFR.
Helical Metering Rotor
Industries: Chemical, Food, Pharmaceutical
This puts a spin on the standard Metering Rotor with its helical grooves. When you need a controlled flow for metering small batches, the slanted grooves break up small batches of material that are prone to clumping. That means a more continuous flow with no material buildup.
Still can’t choose?
They’re all great rotors, but only one will be the ideal choice for your material and system. Contact our team of rotary valve experts to determine exactly which options you need for optimal flow, performance, and lifespan.