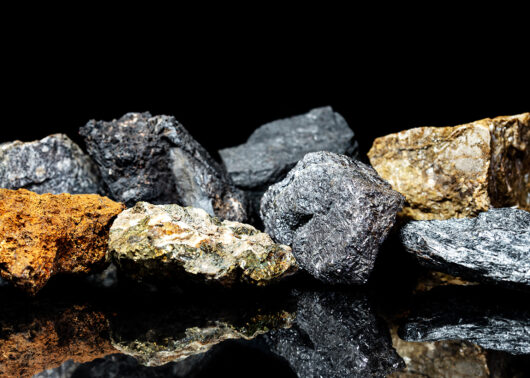
Why do mineral processors make great neighbors? Because they mine their own business.
Now that we’ve kicked off the year with a corny joke, let’s talk about mineral processing. If you work in the industry, you know there are always plenty of changes to navigate — changes in ore quality, regulations, markets, and other issues that can crop up during operation.
Part of the challenge is that the way you convey minerals strongly depends on what they’re made of (the chemical composition) and where they come from (the geological environment). That’s true at any point in the process, whether you’re transforming raw ore into your core products or separating the minerals from waste and other metals.
To get the most value from your raw material, you need a well-designed conveying system and a lot of high-quality data. Here’s what we recommend.
Tip: 1 Know your material characteristics
We always recommend studying the characteristics of any material you’re conveying, because it impacts how the material flows through the system and behaves with different pieces of equipment. This affects all kinds of conveying parameters like pressure levels, product aeration, conveying speed, and friction, just to name a few.
The same goes for mineral ore, especially because its quality can vary, and traits like hardness, density, and particle size can be different from batch to batch. When processed, these ores may also create by-products that have their own properties and behaviors within the system.
We use all these variables to size and configure a rotary airlock valve that will best fit your process. Getting your material analyzed or tested will help you fully understand its characteristics, leading to more efficient processing and fewer problems down the line.
Tip 1.5: Take spodumene, or lithium ore, as an example
Spodumene’s forms include granular, massive (meaning it has no visible crystal structure), and crystalline, and it can contain traces of other minerals such as iron, manganese, and magnesium. It typically has relatively low density, high hardness, and good cleavage (meaning it’s easy to break apart along certain weak planes in its composition). Spodumene also tends to be quite abrasive, making it prone to wearing down conveying equipment more quickly than other materials.
Considering how much one mineral can vary, it’s a good idea to get your product analyzed or tested to understand its exact characteristics.
Tip 2: Find out if your material is combustible
Material analysis can also reveal whether your material produces any particles that may be categorized as a combustible dust. As outlined in NFPA regulations (652 and 654), combustible dusts have the potential to ignite fires or deflagrations, so you may have to make some changes in your plant to stay in compliance. These may include ventilation, dust collection systems, the specifications of your equipment (rotary valves included), and even your cleaning routine.
Tip 3: Monitor your process
When conveying minerals, your process variables include things like feed rate, material characteristics, temperature, and pressure. With so many steps between getting the raw ore to your final product, it’s important to maintain stable consistency, energy efficiency, and quality. You can monitor and control your process with different sensors, tools, and software, and then adjust as needed.
If you’re looking to improve a rotary valve’s energy efficiency, consider one with a direct drive motor. Because they lack the extra friction of a chain drive, direct drives provide higher torque at a lower RPM.
Tip 4: Use tools to optimize the process
Complex industries like mineral processing require dynamic solutions. You may be able to implement mathematical models, software, or even AI tools to simulate your mineral processing flow and measure performance. These types of tools let you run different scenarios and answer questions like, “How does my ore behave in this part of the process?”, “Where are the bottlenecks in my system?”, and “Where can I improve efficiency?” Data is your friend, giving you an in-depth view of your process and helping you capture insights you might otherwise miss.
Tip 5: Choose the right equipment (and valves)
There’s plenty to think about when it comes to processing equipment, so we’ll focus on what we know best: rotary valves. Minerals tend to be quite abrasive, so we recommend features that hold up to the daily wear-and-tear of your process. The goal is to extend the overall lifespan of your valve and prevent any material issues that could clog up or damage your system.
For that, common options include our classic CI Series and MD Series valves, which are highly configurable to complement the unique characteristics of your mineral.
Here’s a quick look at some optional features to consider:
- A closed-end rotor shields the outboard bearings and endplates from extremely abrasive material.
- A rotor with adjustable tips reduces maintenance costs by letting you periodically replace the tips rather than the entire rotor.
- A hard chrome, heavy plate chrome, or Tungsten coating to protect the internals from wear.
- If your material is prone to building up, you can maintain a smooth flow by adding an air purge kit for the shaft seals, rotor pockets, or a combination of both.
- For issues with material jamming, we recommend a shear protector or an inlet shunt and shear pin sprocket.
Bonus tip: Work with a vendor who knows your industry
Knowing conveying systems and bulk materials is a point of pride here at ACS Valves. Give us a call to pick our brains and learn more about how we can help optimize your process with rotary valves.