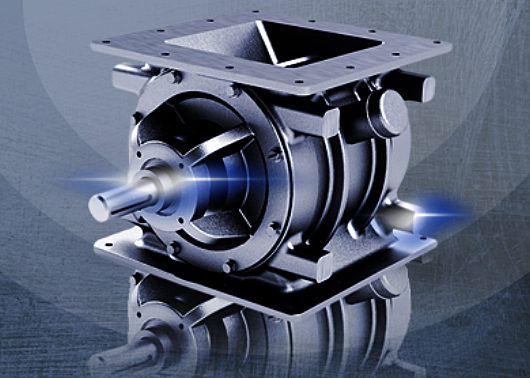
So that they can weather the dust storm
A sandstorm’s a-brewin’ and this time, it’s inside your valve.
Will it chafe in the face on oncoming sand blasts? How much will it pain your production?
A good chafe usually calls for a good baby powderin’, but for valves, applying a simple weather-resistant coat should do just fine.
We recommend protecting them with a coat of hard chrome, Teflon, or tungsten to keep them safe from the effects of dust storms, melted sugar and out of control rocks. Here’s why:
What are coatings and why should I care?
Coatings are a layer that is added to a cast iron valve to protect it from abrasive, corrosive or sticky material.
Abrasive material can cause an increase in the rotor to housing clearance, leading to an increase in air escaping from the airlock, and reduced efficiency. Meanwhile, sticky material can build up and reduce your flow rates. In both cases, you will be facing increased downtime, increased maintenance and lower lifecycles on your valve, meaning you will need to replace it sooner.
Coatings can prolong the life of your valve, by protecting it from wear, as well as allowing sticky material to slide off the surface.
What coatings work with my material?
Sticky materials: Materials like sugar are the first and lightest level of abrasion resistance. They require a hard chrome for the valve’s housing and endplates, and Teflon coating for the rotor. Depending on how sticky the material is, another option for the rotor is a complete 304 stainless steel rotor to sit in the coated housing and endplates. For sticky material this allows material to slide off easier, instead of building up and reducing your flow rate.
Moderately abrasive & corrosive materials: The next level up, materials like cement require a heavy plate chrome. This is the same as a hard chrome, but thicker. This can only be applied to the housing and endplates, which is where a stainless steel rotor would also come into play. Rotors can be easily replaced when they wear, instead of replacing your entire valve.
Highly abrasive materials: Tungsten coating is used for the highest level of abrasion resistance for products like silica sand. The tungsten can coat the rotor, housing and endplates in combination.
Do I always need to coat my valve?
With sticky materials like sugar, there will be more build up the heavier or moister the material is. With powdered sugar the material is more likely to slide off the coating instead of sticking to it, but with granulated sugar, it might be a better idea to invest in an entire stainless steel valve, instead of a coating on a cast iron valve. With stickier materials, if they it get even slightly wet, they will start to harden and cause material build up that will lead to reduced flow rate and reduced efficiencies on your line.
What other factors should be considered?
Take a look at your flow rates, seal types as well as system types to determine how much more abrasion will be happening inside the valve, or how much material will be building up. If the valve is being placed on a pneumatic conveying line that has a higher pressure, you're more likely to see more wear. When the air comes through the valve, it can aerate the material and make it more abrasive.
To go along with coatings, we sometimes recommend slowing your valve down. Material moving too quickly will result in unnecessary wear.
It’s also a good idea to look at your rotor accessories. Air purge seals, for example, keep material away from your housing endplates. Rotor pocket purges are great at keeping sticky materials moving and preventing building up.