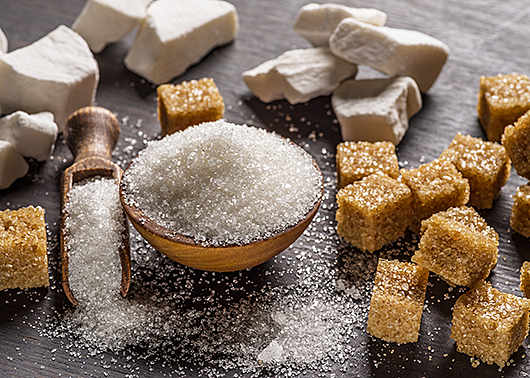
As far as processed ingredients go, sugar seems pretty innocent. It’s good for sweetening a cup of coffee or rescuing your mouth after eating too many hot wings.
In a conveying context, sugar and spice are not so nice. Because their particles are so light and fine (but also dense), they have a habit of sticking together and wreaking havoc on your equipment.
And we’re not only talking about sugar. It could be any light, powdery substance, whether it’s salt, flour, ground nuts, powdered spices, dietary supplements, pigments, cosmetic powders, or even wallboard slurry material.
What’s the big deal?
When powdered materials pass through your conveying line, the motion and heat can cause those fine particles to melt and stick together. That’s how they start building up on equipment — like the internal housing of your rotary airlock valve — and cause premature wear.
In valves, rotors and endplates usually suffer the most damage from fine powders. It’s important to choose the right type of rotary valve and options to prevent unnecessary wear.
OK. What valve do I need?
For faster cleanup, a valve on rails
When you need to clean up quickly, a rail system will never let you down. Rotary valves built on rails make it possible to access the housing in just a few minutes, without having to use tools. This is especially useful in food-grade or sanitary applications where you need to be extra careful about contamination.
The Sanitary MD with Quick-Clean RotorRail™ is a classic example. Just turn the handles, pull out the rotor, and start cleaning. The simple design and stainless-steel housing make it a breeze.
For corrosion resistance, a valve with special coatings
Some of these melty, sticky powders can actually cause corrosion in your rotary valve. Salt is a common culprit. If you go long enough without cleaning, material starts building up in the valve’s interior, which can erode the tips of your rotor or eat away at the housing.
This is what the XTR-CI Series Valve was built for. Coated with a special non-stick, chemically resistant surface, the XTR-CI helps material slide through the valve easily, preventing buildup and corrosion. It’s a tough coat of armor that protects against abrasion. It’s also FDA and USDA compliant, making it another great choice for food-grade applications.
For extra air flow, a blow-through valve
If you have a pneumatic conveying system, a blow-through valve like the Aero-Flow gives your process a big efficiency boost. Designed for dense materials like the ones we’ve covered, the Aero-Flow provides air-assisted material induction into your system through two inlet manifolds.
By mixing your material with pressurized air, it seals key entry points, preventing leaks. It also keeps your material constantly aerated, preventing it from melting or sticking.
Can I customize these?
Yep, our valves have lots of customization options. We already mentioned the best coatings for sanitation and corrosion resistance, but there are many more to choose from, depending on your application.
As for rotors, there are two you’ll want to consider for sugar-like materials. The first is the Radius Pocket Rotor, which has U-shaped vanes to prevent material from building up inside the pockets. It’s so simple it’s kind of genius.
Second, there’s the Bolt-On Serrated Tips Rotor, which is exactly what it sounds like. The serrated tips scrape off any granulated, sticky material as it accumulates on the valve interior.
Now I want candy.
So do we! Before you take a snack break, send an email to one of the friendly reps at ACS Valves. We’ll help you size and configure a rotary valve that works for your process.