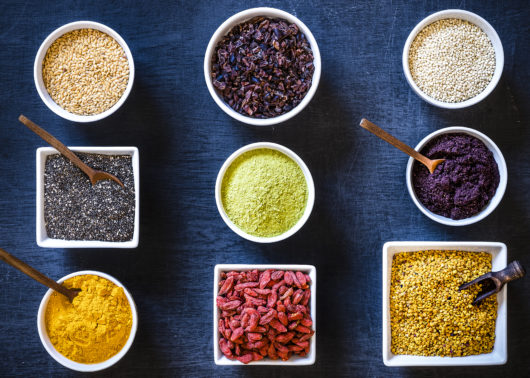
Whether they’re looking to get more nutrition, curb environmental concerns or chase the ever-elusive beach bod, it seems everyone is trying to make positive dietary changes these days.
For a health food manufacturer, that means you’re constantly reading up on new diets — gluten-free, keto, paleo, low-carb, you name it — and thinking about how to incorporate the latest superfoods or trendy ingredients in your products. It also means you’re hard at work.
We respect that work ethic, and we’re here to help you make smart choices in plant layout, equipment and accessories — and whatever helps you save money and time.
First things first: Know your material
Your material characteristics have an impact on everything else we’ll cover here. Materials such as sugar or salt, for example, behave differently than wheat and grains. The first group is more prone to melting, sticking and buildup, while the latter may cause abrasion or be prone to damage.
If you’re keeping up with health food trends, you may find yourself in unfamiliar territory from time to time — each ingredient has unique properties. They react differently to changes in pressure, air velocity and temperature, and they may require different types of equipment to convey efficiently.
In other words, it’s worth having new materials analyzed to fully understand their characteristics.
Facility location
Depending on the location of your facility, you may need engineering controls in place to account for factors like temperature and elevation, which can cause unexpected issues with material flow. Ingredients prone to melting, like sugar, may not do well in a hot location, unless you have the right temperature controls in your facility.
Since you’re working with food, you’ll also want to ensure your plant is not located near a hotspot for pests. Take every possible precaution to monitor and prevent pest activity, because these are major culprits for contamination.
Layout and material flow
All those calculations about material influence the layout and composition of the conveying line. It’s crucial to ensure things flow smoothly and quickly, but also prevent over-feeding the line or overstuffing areas like the rotor pockets of your valve. If you’re conveying multiple materials, you may be thinking about ways to combine, split or divert feeds to make your process more efficient.
There are a few different rotary valves available to help with those types of scenarios. For applications with high volumes of material going into separate feeds, the new Multi-Port Valve has multiple separate airlock compartments to help you do just that.
If you’re simply conveying different materials through the same line, a valve with quick-cleaning features can really speed up those sanitary measures, which we’ll explain more below.
Sanitary features
Chances are you’re working in a sanitary or food-grade application, so you know all about the need to clean surfaces often and minimize contamination. For that reason, stainless-steel materials are standard in this industry, though there may be alternatives or additional coatings suited to your application.
It’s also important for material contact surfaces to be smooth and curved where possible – that is, free of cracks or recesses where material can get stuck. If you compare a standard V-shaped valve rotor to a U-shaped one, you’ll see what we mean: the curved pockets are much easier to wipe down.
Some pieces of equipment come with sanitary features built-in. The Quick-Clean rotary valve, for example, dramatically cuts down cleaning time with its easy-to-use rail system.
Additional equipment and options
There’s plenty of equipment available to prevent issues like abrasion, build-up, material plugging, damage and premature wear. Here are a few quick examples:
- Bakery processing and milling: Rotary airlock feeders help these dense and sticky materials flow through pneumatic conveying systems without building up.
- Wheat and grain: Vacuum blowers prevent these pressure-sensitive materials from getting compacted or damaged. Inlet shear protectors keep them from jamming in rotor clearances.
- Flour, sugar or any ingredient with some moisture content: An air purge kit on the rotary valve prevents abrasion and infiltration and keeps material from sticking.
- Salt and other corrosive ingredients: A corrosion-resistant coating prevents material from wearing down parts and internal surfaces.
There are way too many options to cover in one blog, so talk to an expert to make sure you’re getting the right solutions for your application.
Read up on regulations
Regulations for your application may address sanitation, health and safety, odor emissions from your facility, combustible dusts or all of the above. These will vary depending on your location, so make sure you’re well-versed in the relevant rules.
If you’re working with a new or unfamiliar material, you should have it analyzed to see if it’s considered a combustible dust. If it is, you’ll need to perform regular Dust Hazard Assessments (DHAs) in your plant to keep workers safe and keep up with NFPA compliance.
Work with other experts
Trends change, but the basics stay the same. Health food manufacturers are always ready to pivot their operations to chase new opportunities. Whenever that time comes, it pays to work with experts who are well-versed in all forms of material conveying and processing.
That description fits us to a T. Contact ACS Valves to discuss your new conveying needs and find a rotary valve, conveying equipment or accessory that’s perfect for your application.