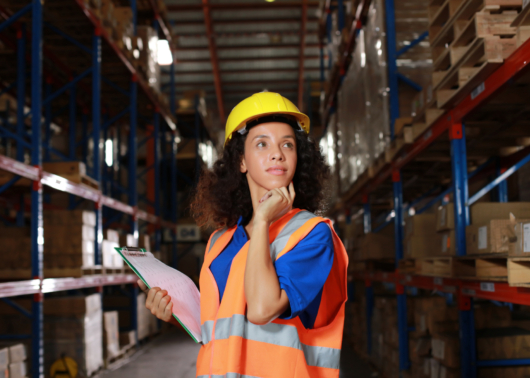
If you ever fell asleep in history class, we won’t fault you. It’s tough to remember who won the Battle of Thermopylae in 480 BC, or why Louis XIV was so obsessed with showing off his legs in classical paintings.
With your conveying line, though, all the details of history matter. A historical maintenance log is essentially a record of all maintenance, replacements and repairs your team performs – something you should be able to easily reference whenever it’s needed.
There are plenty of reasons to do this, but our big three are safety, equipment longevity and regulatory compliance.
It keeps people safe
Some maintenance procedures are about more than production efficiency – they are also in place to keep people safe. Take the humble rotary valve, for example: because of its role as an airlock, it works as an isolation device on your conveying line. That means if a fire breaks out, the valve can stop the flames from spreading further down the line.
It’s even more important that these types of equipment are well-maintained. In the case of the valve, you’ll want to check the rotor-to-housing tolerances every few weeks to ensure they stay below 0.0079 inches (according to the NFPA standard). If they ever rise above that number, they won’t lock out air as effectively, and you will need to replace the rotor to get back into compliance.
To keep everyone safe, review maintenance logs often to ensure these checks are being done on a regular basis. You could also keep a kit of spare parts on hand to make replacements easy.
It helps equipment last longer
Conveying lines have lots of moving parts, and when something goes wrong, it can be hard to pinpoint exactly where the issue is happening. For example, material blockage may happen further down the line, but the cause could be an improperly-sized pressure blower package at the front.
Historical maintenance logs come in handy diagnosing issues. They help staff understand the problem, see what was done on a previous shift, then try new approaches as needed. Because some equipment needs upkeep more often than others, logs also keep track of what has been done so far, helping staff keep everything up-to-date on a regular maintenance rotation.
A proper maintenance schedule is good for the longevity of pretty much any piece of equipment. In our rotary airlock valves, which have CNC-machined components for added precision, regular cleaning and maintenance reduces wear-and-tear on key parts like the rotor and shaft seals.
It keeps your business compliant
Again, some types of equipment function as engineering controls or safety features to protect against hazards. Some of this equipment is required by the NFPA, OSHA, FDA or other regulatory bodies.
In some cases, an auditor or inspector from one of these organizations may want to take a look at your facility. For example, this could happen if your plant processes combustible dusts. Inspectors may look at factors like the conveying line layout, ventilation, safety protocols and equipment to ensure you are in compliance with the NFPA.
Documentation can be a big help in these situations. Show the inspector a historical maintenance log to demonstrate that your people are keeping equipment in good shape, repairing any issues and following procedures.
Keep on logging
There’s a reason why they record the Captain’s Log on every episode of Star Trek. In the manufacturing universe, regular maintenance and proper documentation are essential to running a safe, efficient and compliant conveying line.
Any questions about rotary valve safety or maintenance? We’re well-versed in NFPA compliance and much more, so give us a call if you need more information.