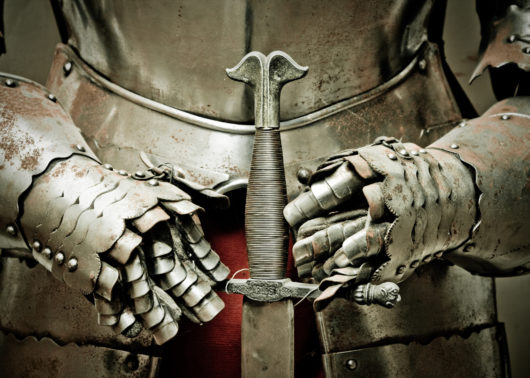
If you could have one superpower — anything at all — what would it be? X-ray vision? Mind reading? The ability to resist corrosion and meet food safety standards?
If that last one sounds appealing, you can’t beat the XTR Series of rotary airlock valves. It’s designed specifically for conveying abrasive or acidic materials, no matter how tough, and it complies with FDA and USDA standards for food-grade applications.
Did you know Superman’s cape is nearly indestructible? The signature coating on the XTR Series valve, called XTR-Coat, is a lot like that: it extends the valve’s lifespan by providing key protection against corrosion and food build-up. For you, that means spending less downtime and money on maintenance and replacements.
If your equipment wears out quickly or needs repairs often, the XTR Series might be the perfect rotary valve to come to the rescue.
Where the XTR Series saves the day
The XTR Series valve excels in pressure pneumatic conveying systems, particularly those requiring high corrosion resistance or food-grade product contact.
Heavy-duty applications such as gravel and cement are extremely tough on valves that aren’t properly equipped. The same goes for corrosive chemicals and acid. The XTR-Coat, a chemically-resistant coating, protects the valve’s internals and rotor from wear-and-tear.
Food applications are tricky in a different way — fine, sticky materials such as sugar, flour and some pet food ingredients are classic cases for build-up. As material accumulates inside the valve, it causes problems with the flow rate, pocket fill and possible contamination. XTR-Coat’s non-stick surface helps material slide off and makes the cleaning process easy — and it works well in washdown-duty environments.
Salt is one example of a material that needs help on both fronts: it’s corrosive and prone to sticking. In each case, material wears down the valve’s rotor and internals, making it necessary to replace parts more often and reducing the valve’s overall lifespan. The XTR Series is designed to save you money and downtime by preventing all that damage.
A few other things to know about the XTR Series valve: it resists temperatures up to 500°F. It also features non-toxic, non-porous, moisture-proof surfaces and mold release.
What else can I do about corrosion and contamination concerns?
The XTR Series valve is available with a square or round flange, and it can be sized and customized to fit your process. That means you can configure different aspects of the valve to better suit your material — whether it’s sugar, gravel, paint pigment or salt — and your application.
With that in mind, a rotor with U-shaped pockets is a useful swap for the standard V-shaped rotor. The V shape is more prone to material getting stuck in the crease, which leads to build-up, compromised material flow and contamination. Without cracks or crevasses, the U shape helps material slide through easily and is much easier to wipe clean.
Regular cleaning, by the way, is an essential step in avoiding material build-up and corrosion. The same goes for maintenance. Use glandless shaft seals to avoid the usual cleanup and contamination risks from bearing seal leaks. While you’re at it, a direct drive package also helps avoid contamination (and reduces maintenance time) because it doesn’t require the same constant lubrication as a chain drive.
But what works best for me?
Don’t worry — you don’t have to figure it all out on your own. An ACS expert can tell you more about choosing the right valve, configuring it with the right parts and accessories, and boosting efficiency in your conveying system. If you have concerns about regulatory compliance — whether it’s FDA, USDA or NFPA — we can help you there, too. All in a way that fits your budget. Let’s have a chat!