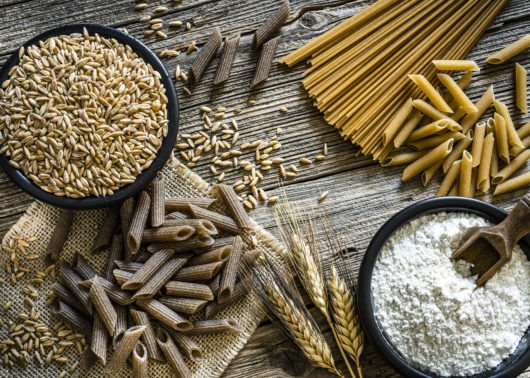
You’re a miller, born and bread. A cereal miller, you might say. Corny puns aside, here’s a small kernel of truth: you need to be a tough nut to work in a mill.
First off, you’re part of a food processing tradition that evolved over thousands of years. The industry has come a long way since the days of hitting grains with rocks.
These days, there are a lot more mouths to feed — not to mention a tight profit margin to worry about. It makes sense that today’s millers want more ways to boost production efficiency, keep costs low, promote food safety and reduce workplace hazards.
As a key piece in the modern conveying line, rotary airlock valves have a big role to play in all this.
Milling rotary valve choices
Because mills can handle such a wide variety of ingredients, let’s start with the basics: where will the rotary valve be placed on your conveying line, and what types of ingredients are you conveying? Think in terms of material characteristics like density, size and abrasiveness.
For more granular materials
Examples: Wheat, corn kernels and raw oats.
At the earlier stages of processing, your wheat, corn or oat products show up in the form of larger granules. These materials are larger with harder edges, making them abrasive and more likely to wear down your equipment. They can sometimes consume more energy, but there are ways to make them less of a strain on your mechanical conveying system.
In this case, a valve with special coatings comes in handy. The XTR-CI and XTR-MD Series are two highly versatile, customizable rotary valves that benefit from the protection of XTR-Coat. This USDA and FDA-approved coating protects the valve from abrasion and prevents more powdery particles from sticking to the internals. For you, that means a longer lifespan, more efficient flow and less time spent on maintenance.
For powdery materials
Examples: White and whole wheat flours, cornmeal, buckwheat flour, and ground nut flour.
Whether they’re going into pasta, bread or delicious pastries, all these different types of flours have similar material characteristics. Because they’ve been processed by this point, the granules are lighter and finer, but still dense enough to stick together and build up on your equipment.
The XTR is another good choice here, but if you’re looking to speed up the cleaning process, a valve built on rails is the way to go. A rail system provides quick access to the rotary valve’s internals, requiring no tools and no intensive process to dismantle it.
Blow-through valves are another strong option for these sticky, dense materials, which are typically conveyed in pneumatic systems. In this example, the dual-induction design uses pressurized air to help move powders through the valve without melting or sticking.
For multi-ingredient feeds
Because many mills produce multiple varieties of similar ingredients, it may make sense to give your conveying system a split-feed configuration – for example, when wheat processed in one line splits into a line each for bleached and unbleached flour.
That’s where rotary valves with multiple compartments come in handy. This video shows how a long, trough-inspired valve conveys material through separate compartments with independent drives. With the right coatings and rotors, it could be just what your mill needs to streamline processing.
Don’t forget to accessorize
To help material flow properly, your valve should have a rotor that works well with the size and shape of your ingredients. We’ve covered a lot already, so here’s a rapid-fire list to get you started:
- Rotors with U-shaped pockets that are easier to clean
- Rotors with serrated tips that scrape off material buildup
- Rotors with closed ends for more abrasive grains
- Rotors with small grooves for metering test batches
You can browse all the options here. Since we’re talking about material that is powdery or leaves dust behind, it’s worth mentioning air purge kits as an accessory. They send compressed air to key areas of the rotary valve – the shaft seals, the airlock rotors, or both – to prevent buildup.
Take the first step
We owe mills a lot for making so many of our favorite foods. For help and advice that makes your job easier, contact ACS Valves to size, design and configure the perfect rotary airlock valve.