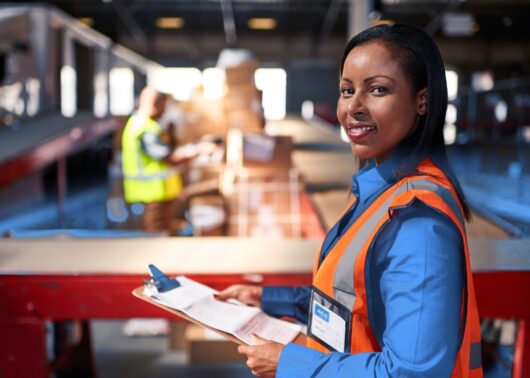
No prizes for guessing what we do here at ACS Valves. (But if we were going to give you a prize, it would be a nice blue ribbon.) Though we’re focused on making rotary airlock valves, we started out manufacturing entire pneumatic conveying systems.
Yup, ACS stands for Ancaster Conveying Systems. Why did we switch to valves?
- We’re really good at making them.
- Like the valves in a human heart, they are critical to the system’s overall performance.
- We knew other manufacturers could benefit from our valve R&D.
We’re proud of our history. Over the years, we’ve gained invaluable conveying expertise, both through our own work and through working closely with bulk material processors like you. Everything we know about conveying is channeled into designing, building, and configuring rotary valves.
In many ways, manufacturing is a team sport, and we do our best to set you up for plenty of goals. Here’s how.
1) Equipment needs to play well together
To perform at their best, rotary valves need to integrate well with the rest of the conveying line — and vice versa. Proper sizing and specifying is critical, otherwise you could end up with material flow issues, leaks, shorter maintenance cycles, or even safety hazards.
That’s why we always ask for details about your system, as well as your application and material characteristics, before recommending a valve.
2) We’re troubleshooting detectives
Thanks to our system knowledge, we can troubleshoot issues based on signs like heat, vibration, how material behaves while going through your valve, how it works with the equipment above or below it, and even what type of noise it’s making. Yup, we can diagnose a rotary valve just by listening to it. I guess you could call us valve whisperers.
Whether it’s related to your material, the valve’s installation, a worn-out part, or another piece of equipment, we can help you pinpoint the issue and resolve it quickly.
3) We can customize the right valve for you
We like to say that no valves come off-the-shelf here at ACS Valves, because each conveying system is unique and requires its own tailored solution. We’ve seen what types of problems can arise when a “standard” valve is put in a specialized situation, from material jams to frequent repairs.
That said, we don’t expect you to know exactly what you need out of the dozens of rotors, coatings, and other options we offer. Our reps will walk you through the best options.
4) We are constantly testing for quality
To ensure each rotary valve performs well as a component in a real processing environment, we factory test it in an actual conveying system. We also put each valve through a 46-step test before shipping. If the valve fails 1 out of 46 tests, it’s not good enough. That’s how you know you’re getting a 100% trustworthy piece of equipment.
5) We’re big on innovation
Sometimes your conveying issues really stick with us (pun intended), and we decide to come up with smarter solutions to application-specific challenges. That’s how our engineers came up with several inventions in rotary valves and accessories, including the Quick-Clean Valve on RotorRails for easy cleanup, the sleeve-style shaft seal to prevent contamination, the XTR Series for extra corrosion resistance, and the Multi-Port for split feed conveying lines.
You’re an important part of that innovation. By listening closely to our customers, we come up with ideas that boost productivity in their systems, whether it’s by reducing downtime, stopping leaks, minimizing maintenance, or improving safety.
How can we help?
At heart, we are still conveying systems aficionados as much as we are rotary valve engineers, and we’ll keep improving our valves because we care about optimizing your entire line.
Have a system-specific question? Contact ACS Valves – we’re more than happy to help.