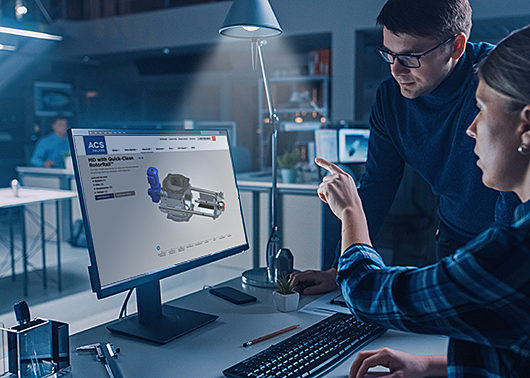
According to legend, Nikola Tesla was born during a lightning storm. A fitting story for an inventor who went on to make historic contributions to the electricity supply system.
You might say ACS Valves was born in a manufacturing plant. Okay, not literally, but our founders worked in conveying for many years before establishing the company. We even manufactured entire pneumatic conveying systems before narrowing our scope to rotary airlock valves.
Why did we laser-focus on valves? It turns out we’re really good at making them, but we also saw firsthand how critical valves are to the performance of the overall system. We figured there were plenty of manufacturers who could benefit from our years of R&D.
Thanks to our decades of experience working with conveying systems, we also developed some rotary valve innovations that help our customers address key challenges.
Maintaining clean machinery with RotorRails
Standard rotary valves can get heavy – sometimes up to 2,500 lbs – and take longer to dismantle. In sanitary applications like food, pet food, and pharmaceuticals, that can add a lot of downtime when you need to clean your equipment.
We developed RotorRails, a rail system for valves, to make cleaning quick and painless. You don’t need any special tools to open it up. Just unlatch it, slide the rotor away from the housing, and start wiping down the vanes. It’s a real time-saver for our customers.
Keeping options open with the Multi-Port
The Multi-Port valve was born when one of our engineers looked at a standard trough-style feeder and thought, how can we make this even better? He took that basic framework and designed a valve with multiple compartments.
Why? To give your conveying system even more flexibility. The Multi-Port excels in cases where you have split feeds running simultaneously – or when you just need a few backup compartments to keep production moving in any situation. It’s also a big improvement in terms of NFPA compliance, as the smaller compartment sizes make it easier to maintain the required tolerances.
Preventing leaks with sleeve-style shaft seals
We learn a lot just by talking with customers (and really listening). When they mentioned the need to prevent contamination and messes caused by leaks, we developed a special shaft seal with three quad rings and a Teflon seal.
This shaft seal protects the rotary valve’s bearings by creating a tight seal in the area. It lasts longer and eliminates static electricity (sorry, Tesla). Compared to traditional packing glands, it’s also much easier to install and replace.
Standing up to corrosion with XTR-Coat
After helping customers with countless types of tricky ingredients, we decided to tackle a specific sticky situation: the problem of fine, dense powders that stick to equipment and slowly corrode it.
Salt and sugar are two prime examples. We introduced the XTR-Coat, a specialized coating that helps those ingredients slide through the valve with ease. Think of it as an armor that prevents troublesome build-up and protects the rotor and housing from corrosion.
Using our knowledge to benefit you
Though we’ve helped plenty of customers with our innovations, there’s no one-size-fits-all solution for a specialized conveying system. We configure every single one of our valves to integrate well with the application, the material, and the system. Beyond that, we constantly keep our eyes and ears open to new ideas – always searching for ways to help the manufacturing industry work smarter, not harder.
Have a unique conveying challenge for us? Let’s talk about how our valves can help.