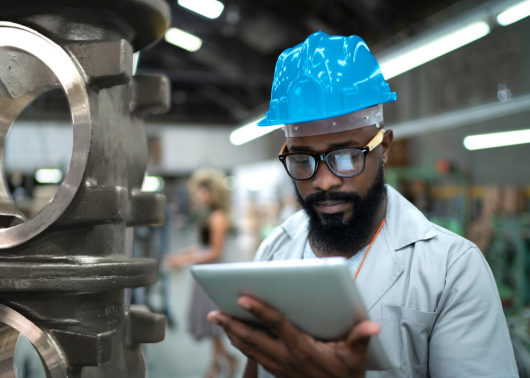
When it comes to plant safety, processing efficiency, and the ultimate quality of your end product, every piece of equipment in your conveying system matters.
Rotary airlock valves are kind of like the valves we have in our hearts – they connect different pieces of equipment to ensure material flows safely from one component to the next. Without a properly functioning valve, you risk problems like material loss or flow issues.
This gets trickier when you’re handling combustible dusts, because material leakage increases the risk of dust explosions or deflagrations in your plant.
How do you keep valves safe?
To keep your system safe and efficient, we perform a 46-step inspection on each rotary valve that leaves our manufacturing facility. Like your conveying system, each part of the inspection is important to ensure the valve performs at its best.
That’s why our expert inspectors need to sign off on each step of the inspection before a valve proceeds to the next step of the manufacturing process.
What’s included in the inspection?
We inspect each individual part of your rotary valve at different stages, including:
- Endplates
- Bearings
- Rotor assembly
- Housing
- Drive guard assembly
- Drive mounting base
- Drive package
- Sprockets and chain
- Speed switch assembly
- Final valve assembly
- Paint
We also test the valves for several components at each stage, including:
- Casting construction
- Condition of casting before and after machining
- Correct sizing and tolerance on various parts
- Chrome plating
- Cosmetic appearance
- Clearances
- Quality of welding
Because our valves are custom designed to optimize performance in your application, the specific components we inspect will vary.
How do the tests work?
We perform live tests in a factory floor setting, running the valves to ensure everything is working correctly, including all mechanical and electrical components. We check that the gearmotor is working well and running at proper amperage, and we record the amperage readings for reference.
The live tests also include checks to make sure the valve is rotating correctly and running as it should be. Our inspectors then check rotor tip clearances and side clearances on the top inlet flange.
Everything we note in our tests is recorded on an inspection sheet for proper record keeping.
What happens when the valve is ready to ship?
At the shipping stage, the valve is inspected again to make sure all the data corresponds to the bill of materials. Our quality control manager performs a rigorous quality check before each valve is shipped out.
Safety stickers and rotation stickers are placed on the valve as well. Inspectors take a photo of the valve, and then it is securely fastened to a skid with steel banding and protective shrink wrap.
Do you test for regulatory compliance?
At ACS Valves, we design rotary valves in compliance with the National Fire Protection Association (NFPA) and the Occupational Safety and Health Administration (OSHA) as a standard.
Some typical compliance features include safety covers, an 8-vane rotor, and outboard bearings, but we may have other recommendations depending on your application and material.
Can I see the inspection documents?
Absolutely. All inspection documentation is available on request. If you need help with a technical issue, feel free to contact our knowledgeable support staff. We’re here to help!