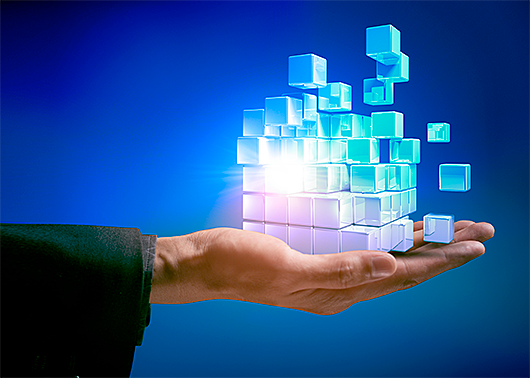
“A lot of people think an airlock’s an airlock, but it’s the configuration of the airlock that really makes a difference.”
That’s the wisdom of Herb Nagy, an expert in rotary airlock valve design. Nagy has been part of the ACS Valves sales team since 2019, and he has been designing and configuring rotary airlock valves for more than 50 years. He knows airlocks like the back of his hand.
“The airlock is the heart of the system. If it’s not configured correctly, the system’s not going to work well,” Nagy explains. “At ACS, we know how to configure the airlock, and that’s how we end up with satisfied customers.”
When he starts quoting a rotary airlock valve, Nagy considers the material, its characteristics, how it’s being fed, where it’s going, and temperatures above and below, to name just a few factors.
Material is the biggest consideration. Airlocks are used to convey a vast range of materials — anything from titanium dioxide powder to plastic pellets to full-sized pop cans.
With the material in mind, Nagy can determine the efficiency and sizing of your rotary airlock. “We can only turn an airlock so fast depending on what the material is,” he says. “Materials like carbon black powder are very fine and almost turn to smoke, so if we turn our airlock too fast, our efficiency goes to pot. If you’re conveying sawdust, you’re getting into a larger airlock.”
Nagy has spent years testing how different materials react in a pneumatic conveying line. When he goes over the application with a new customer, he can quickly narrow down the options to determine the perfect airlock.
Getting into the nitty-gritty
Because no two applications are ever the same, Nagy has designed airlocks for almost every conveying scenario you could imagine.
For example, one customer uses a pneumatic system to convey scrap metal from a CNC machine. The long, coily pieces of scrap have to flow into a semi-trailer for transportation to their foundry, where the material is recycled.
“We put special rotors, shear protectors, and cavity purge on the endplates to keep buildup [out of the valve housing],” Nagy says. “We also set it to 50% efficiency. They last maybe a year and a half.”
That’s a long time for such an abrasive application. In other abrasive industries like cement, asphalt, or limestone, or where materials are conveyed at high temperatures, rotary valves may need special coatings or materials of construction. When designed correctly, valves in these industries can expect a lifespan of at least one year.
When rotary valves are designed incorrectly by another supplier, ACS Valves is sometimes called in to help, as in one case with a cement company in Nebraska. “The airlocks weren’t set up for abrasion – they should have had hard chrome, so the clearances opened up,” Nagy explains. “When that happens, the airlock is inefficient in about six weeks.”
It’s also very important to control the valve’s rotation speed and flow rate. In another case, a customer was working with a sawdust system mounted on a trailer, taking excess sawdust to their chicken coops to prepare for new batches of chickens. After running it successfully for one day, the customer had issues with material buildup in the system.
They called Nagy, and he was ready and willing to help.
“I got the call in Keokuk, Iowa on the Mississippi river, and I ended up in Kansas later that day,” says Nagy. “I saw that they were running an airlock at about 20 RPM – running it too fast, which made the air blow back up and slow everything down. We got it to about 80% efficiency on the airlock. We solved the problem, and they were tickled to death.”
Valves with value
When you order a rotary airlock valve from ACS, the process is very much a conversation between you and our team. A rep like Nagy then takes all the factors we mentioned into account, along with anything unique about your system, and determines the most efficient airlock design. He also takes the time to explain the reasoning behind his recommendations, so you always know what to expect.
We understand the importance of sticking to production schedules, so we communicate closely about the engineering and shipping timelines. Because of the shorter lifespans we mentioned for very abrasive applications like asphalt, we carry plenty of stock that’s ready to ship, so you don’t have to wait long when you need a replacement.
To get the most value out of your new airlock, Nagy has one last bit of wisdom: make sure you perform regular maintenance.
“This rotary airlock isn’t a sledgehammer,” he explains. “It’s a precision machine built to your application, and it has to be maintained.”
Maintenance helps prevent common problems such as material buildup, flow issues, and wear on the machine, which extends its overall longevity.
At the end of the day, as long as we understand your application, our team can make sure you get the best airlock on the market.
Ask and ye shall receive
If you have a question about rotary airlock valves, Herb Nagy is sure to have an answer for you. Feel free to contact him or check our directory of ACS Valves reps to find a valve expert near you.