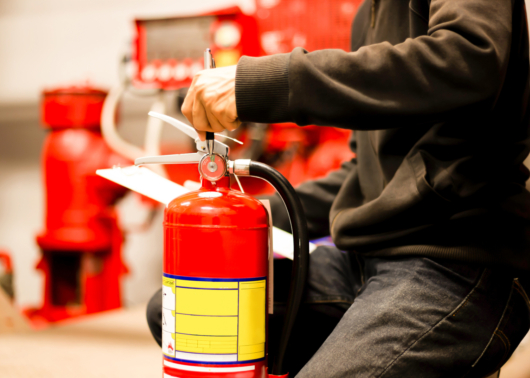
It’s a dusty world we live in — the world of bulk material processing, that is. Whether it’s flour, wood fiber, powdered pigment or metal dust, there are all kinds of ways particles can float into the air or accumulate on surfaces around your processing plant.
Combustible dusts are just part of the job, but it’s very important to keep them in check, because they can ignite to cause a fire, explosion or deflagration at a moment’s notice.
Between 2017 and 2021, U.S. fire departments handled an estimated annual average of 36,784 fires at industrial or manufacturing facilities, according to an NFPA report. These fires created annual losses estimated at 22 civilian deaths, 211 civilian injuries, and $1.5 billion in direct property damage.
Rotary airlock valves are an integral part of dust fire and explosion prevention. If a fire breaks out on your conveying line, a valve will act as an isolation device to stop the spread of flames.
Here’s what we recommend for any NFPA compliant valve.
A quick rotary valve NFPA checklist
Check rotor-to-housing and rotor-to-endplate clearances. Make this a regular part of your maintenance schedule and check to ensure tolerances stay under 0.0079’’ (though 0.004’’ – 0.006’’ is best).
Specify ACST-4 shaft seals. The sleeve-style design eliminates static electricity, reduces frictional heat and prevents build-up around the outboard bearings (which could cause failure if left unattended).
Replace rotors, shaft seals and bearings regularly. This will help you maintain proper tolerances and prevent the type of material build-up that can cause combustible dust to accumulate.
Make sure two or more rotor vanes are in contact with the valve housing at all times. We suggest an 8-vane rotor, but 10- and 12-vane models are also available.
Specify the right rotor blades and tips. The standard for compliance is a 3/8’’ thickness with steel rotor tips. Avoid rubber rotor tips, which sometimes appear on adjustable blades.
Run valves at a low tip speed. This will prevent a possible ignition source.
Design systems with proper ventilation. The rotary airlock should be properly vented, or else air can flow back up into the hopper and blow material dust into the workplace atmosphere.
Keep up with NFPA guidelines. Look at NFPA 68, 69 and 652 in particular, and always specify valves in accordance with these guidelines.
Perform DHAs when needed. Dust Hazard Assessments will help you spot any potential hazards in your facility and identify ways to correct them.
Download or print the NFPA Pocket Guide. You can fold it up and keep it in your pocket for easy access to these tips and more.
What else can I do?
Other than combustible dusts, fires are commonly caused by hot work, flammable liquids and gases, equipment and machinery, and electrical hazards.
Besides choosing compliant equipment, all employees should be trained in emergency escape procedures. Housekeeping is equally important, as regular maintenance will prevent any tools or equipment from malfunctioning and creating potential ignition sources. You can check our NFPA resource page for more handy tips.
NFPA compliance can be tricky, but we’re always happy to help where rotary airlock valves are concerned. Contact ACS Valves to order an NFPA preventative maintenance kit or ask about our rotary valves, which come with plenty of NFPA compliance options.
Updated February 2025.