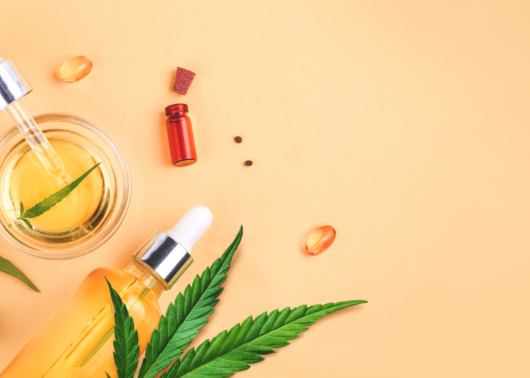
There are plenty of obvious jokes to open a blog about cannabis processing, but we’re going to take the high road. (Sorry.)
Cannabis keeps growing in popularity, but the world of manufacturing cannabis products — whether it’s oils, capsules, edibles or others — is still uncharted territory for many. With such sensitive plants in their care, cultivators need to follow strict rules about lighting, pests, water, temperature, humidity, you name it.
Cannabis processing shares some similarities with cultivation, but it is a different beast. These cannabis processing tips will get you thinking in the right direction.
1) Always follow protocol
It all starts with your location. Depending on the rules in your country or state, you’ll have different regulations to follow for sanitation, recall processes, training, equipment and plant layout, to name a few. Your first step is to familiarize yourself with those laws.
Your health and sanitation protocols are important to establish and enforce from day one. In industries where potential contamination or cross-contamination are a concern, properly equipping your employees is one of the best steps you can take. Make sure they have the right garments, follow strict handwashing and personal hygiene practices, and observe any other cleaning and decontamination protocols you might have.
2) Keep a controlled environment
Location may also influence any measures you take to control the environment in your facility. If your product needs specific temperature and humidity conditions to stay intact as it goes through the conveying line, you’ll need to have the right heating and cooling systems in place. You may also need an odor control system to keep cannabis smells from reaching your neighbors.
Keep an eye on all these systems with calibrated monitoring devices. Again, you should be as familiar as possible with regulations in your area, because laws about things like water runoff, odor emissions and sanitation vary widely.
3) Think about airflow
Proper air filtration and ventilation systems will eliminate airborne contaminants such as bacteria, mold, yeast and pollen. Use HEPA filters for air entering the cannabis production areas and HEPA or activated carbon exiting those areas, which will help with the odor emissions issue.
Bonus tip: If your facility handles combustible dust, good airflow and ventilation will go a long way to keep your workers and equipment safe. Have materials analyzed for combustibility and conduct a Dust Hazard Assessment (DHA) to ensure your setup is NFPA compliant.
4) Sanitary surfaces
The surfaces of floors, ceilings, walls and everything in between can be designed to prevent contamination. They should be hard, durable, resistant to chemical degradation, and sealed without pores, cracks or crevices. Those combined properties keep material from shedding into your product or, conversely, having product build up on surfaces.
Various materials, coatings and coverings are best for sanitation, such as clean room panels, PVC, stainless steel, fiber-reinforced plastic, polyurethane and epoxy.
5) Easy-to-clean equipment
Remember what we said about non-porous surfaces? The same goes for your conveying equipment. Any surfaces that touch your product should be smooth, free of cracks and crevices, and made or coated with material that makes it easier to clean, sanitize, validate and inspect.
The Quick-Clean rotary valve is a good example. It’s built on a rail system to make cleaning easier (think minutes instead of hours), and its standard housing comes in 304 or 316 stainless-steel. The Quick-Clean can be configured with a U-shaped rotor and specialized coatings for different applications.
Is there anything else I should know about valves for cannabis?
Plenty, but you don’t have to learn it alone. Call ACS Valves to get in touch with a friendly rep who can walk you through the best rotary valve configuration for your process.