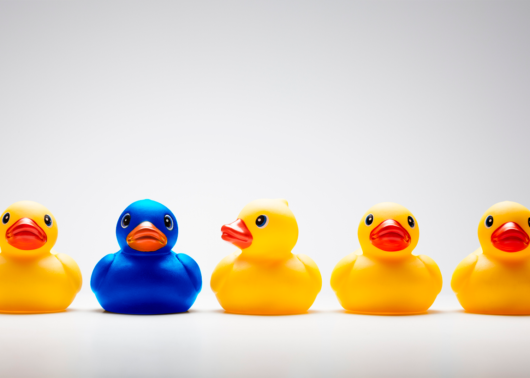
Did you know rubber ducks are actually made of plastic? If you work in the plastics industry, maybe you did know that. You’ll also know how important it is to keep plastic pellets intact until they’re ready to be molded into something new, whether it’s packaging, automotive parts, or a rubber duck worthy of the bubbliest bath.
Pelletizing is a meticulous process. To avoid damaging the plastics that took so much care to form – including precise cuts, temperatures, and timing – you need to choose conveying equipment carefully.
That includes valves. Choosing the right rotary airlock valve helps improve product uniformity, reduce maintenance, and deliver a consistently high-quality product.
Why is pellet shape so important?
There are so many fun names for the things that can go wrong during pelletizing: dog bones, elbows, angel hair, popcorn, dimples, voids… but once they get to a conveying system, they’re anything but fun.
As with most things, input affects output. Even after you’ve solved all those initial issues and formed the perfect pellets or resins, they still need to stay in a consistent size and shape throughout the conveying process.
To keep everything uniform, some standard rules include specifying an accurate rotation speed or flow rate, keeping temperatures and pressures stable, reducing friction, and generally preventing material from getting too bunched up inside the system.
That’s because pinched, shorn, or melted pellets can disrupt material flow and get stuck in your equipment, resulting in more maintenance and shorter lifecycles.
Once they get to the molding stage, if the size or shape varies too much, plastics will melt at different rates and resins won’t create identical parts. That means quality issues for your buyer down the line – a two-headed rubber duckie, anyone?
What types of valves keep pellets intact?
The key is to avoid friction and material drag, which is how pellets can cluster together, get damaged, and jam material flow. Rotary valves with completely smooth surfaces help to avoid material drag. At ACS Valves, our valve housings are cast from high-quality steel, so they have no cracks or crevasses where materials can get jammed or pinched. The same goes for our CNC-machined rotors and parts.
For the plastics industry, we often recommend our most customizable valves, the CI Series (with a square inlet) and the MD Series (with a round inlet). They also come in sanitary and Quick-Clean models for food-grade applications.
The S-Pellet Series is another great option designed specifically for pellets, beads, and granules. It’s designed with a side inlet and adjustable controls to ensure the rotor pockets fill at a consistent rate without shearing materials.
What are the customization options?
The customization options for your rotary valve depend on parameters such as your flow rate, conveying pressure and temperature, and the pellet shape and density. A valve expert can make the best recommendation based on your specifications.
Here are some common suggestions for conveying plastics:
- A rotor with staggered pockets provides a more accurate flow rate.
- For plastic flakes or chips, a rotor with closed ends prevents jamming and protects the outboard bearings and endplates.
- An inlet shear protector prevents material shearing.
- An air purge kit keeps materials from building up in the shaft seal or rotor pocket area.
- A special coating helps pellets flow smoothly and protect the valve’s internals from wear.
How else can I prevent material issues?
Once you have the right valve design, it’s all about regular maintenance. You should check the rotor-to-housing tolerances every few weeks to ensure they stay within the right range. If the tolerance increases too much, pellets can start to get jammed or dragged inside the housing.
That’s when it’s time to replace the rotor. Keep a historical maintenance log to get an idea of how often it needs to be replaced so you can order new parts proactively or get our NFPA kit to have all the most crucial spare parts on hand.
Anything else I need to know?
There may be something unique to your application that affects your optimal rotary valve configuration. Speak to an ACS Valves rep
to get the best recommendation for consistent flow, better material integrity, and a longer lifespan for your valve.