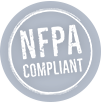
XTR-MD Series
Corrosion-resistant Rotary Valve for Abrasive or Acidic MaterialsThe XTR-MD Series valve boasts high corrosion resistance with the same efficient, high-performance design of our popular round-flange MD Series rotary valve. It is specially outfitted to excel in any pressure pneumatic conveying system that requires food-grade product contact.
Features & Benefits:
- Cast iron housing and endplates coated with XTR-Coat, a chemically-resistant coating.
- Resists wear and corrosion from chemicals, acid and abrasive material.
- XTR-Coat also prevents material sticking and buildup on valve surfaces.
- USDA and FDA compliant.
- Mild steel or stainless steel rotor machined with precision for tight tolerances.
- Rated for great performance in operating temperatures up to 500°F.
What to do if your valve becomes uncompliant (Because it will)
ACS now offers XTR-Coat synergistic coatings to maximize performance in a variety of applications. XTR-Coat finishes provide wear and corrosion protection, reduced friction and non-stick performance. XTR-Coat finishes are a high-performance, non-toxic and FDA-compliant alternative to industrial chrome plating.
- Handles pressure differentials up to 15 PSIG.
- Available sizes: Round flange 4" through 16".
- Expedites cleaning and sanitation operations; works well in washdown duty environments.
- Non-stick, food-grade properties for sugar, flour, pet food and other food processing applications.
- Dry-lubricity.
- Non-porous, moisture-proof surfaces and mold release.
Rotary Valve Capacity (Cubic Feet/Hr.) | |||||||||||
![]() |
|||||||||||
8 | 12 | 60 | 96 | 120 | 144 | 168 | 192 | 216 | 240 | 264 | |
10 | 24 | 120 | 192 | 240 | 288 | 336 | 384 | 432 | 480 | 528 | |
12 | 45 | 225 | 360 | 450 | 540 | 630 | 720 | 810 | 900 | 990 | |
1 | 5 | 8 | 10 | 12 | 14 | 16 | 18 | 20 | 22 | ||
Rotor Speed (RPM) |
Pharmaceutical and Cosmetics Blogs & Videos
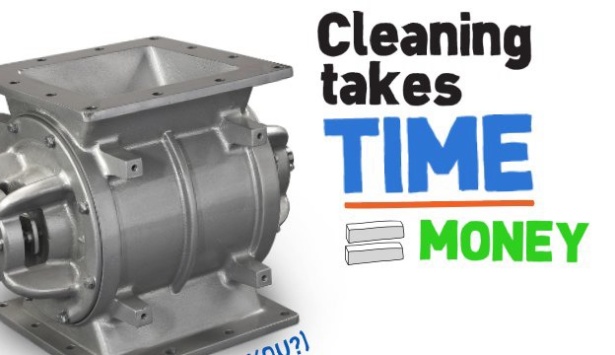
Featured video
Make cleaning suck less with our Quick-Clean valve on RotorRails™
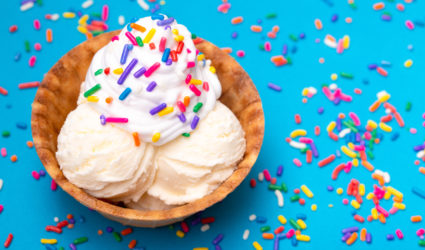
Featured blog
Avoid sticky situations with a rotary airlock feeder
The Aero-Flow feeder valve mixes material with pressurized air to prevent premature wear and boost consistency