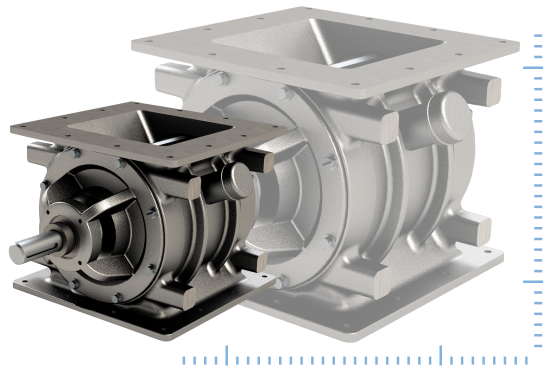
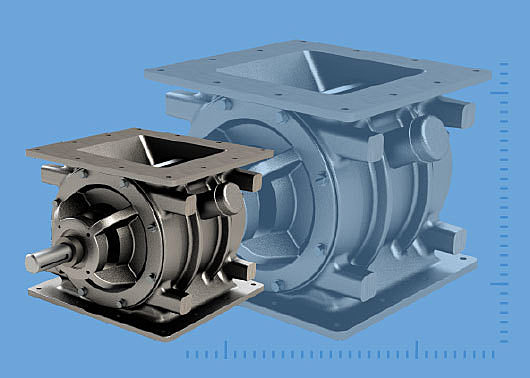
Rotary airlock valves come in an amazing range of sizes, from 500-pound whoppers to small-batch models so tiny they’ll fit in the palm of your hand.
You’ll need expert help to get the size just right — or this new rotary valve sizing tool we launched.
You can go right to the tool to get started, but if you’re looking to understand valve sizing a little bit better, we distilled the essentials down into a handy guide.
Why does size matter?
To get the most efficient rotor pocket capacity and consistent material throughput, accurate rotary valve sizing is essential. Depending on your material, the right size can also help extend the valve’s maintenance cycles and lifespan — for example, by preventing material from building up on the inlet flange, or by reducing wear in more abrasive applications.
Some key terms defined
Designed Conveying Rate
This is the rate at which you convey material through your rotary valve, also called the capacity. If you give us the value in pounds per hour (PPH), we’ll convert it into pounds per minute to make our next set of calculations.
Material Bulk Density
Each material has a bulk density measured in pounds per cubic feet (PCF). Denser materials behave differently than finer materials, which impacts the valve’s capacity and throughput (more on this below). Because PCF is often expressed as a range, we use the lowest value in the range to accurately calculate the rotary valve size.
With the bulk density and pounds per minute we learned above, we can figure out the cubic feet of material that gets conveyed through the valve each minute.
Expected Efficiency of Airlock
Efficiency is also known as pocket fill, or the percentage of material that fills each rotor pocket as the valve turns around in its housing. Your average material does well at 70% efficiency, leaving enough air in the pocket to help your material flow through smoothly. Pellets are usually sized at 50% because they are denser and more clunky, meaning they are more prone to jamming up the system.
Design RPM and Size
With efficiency we get the design rotations per minute (RPM), which is the valve’s effective speed while running at that size. The size refers to the diameter of the valve’s opening, usually called the flange or inlet.
If we get multiple results for the valve size, we generally pick the smaller option. In some cases, like with abrasive material, we recommend upsizing the rotary valve in order to lower the RPM and gain more volume per rotation. This helps extend the valve’s longevity by minimizing wear and tear.
What else affects sizing?
While we created our sizing tool based on some general rules about conveying material through rotary valves, there are a lot of application-dependent factors in valve sizing.
Material characteristics play a big part, especially when it comes to density. A light, fluffy ingredient like flour has a lower PCF than cement, for example, and both will be conveyed at different settings (such as speed, pressure, aeration and pocket size) to account for material density.
Beyond material characteristics, you may have other process requirements — such as multiple conveying line feeds, NFPA compliance or the need to swap ingredients quickly — that affect the size, model and configuration of your rotary airlock valve. That’s where an expert comes in handy.
Meet our human calculators
The sizing tool is a helpful starting point, but our team can really get into the nitty-gritty of options and customizable features to make your rotary valve run as efficiently as possible. Whether you have questions or just want to get started with an estimate, give ACS Valves a call.