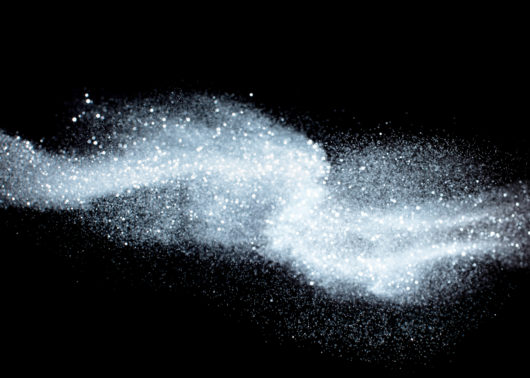
Powders and bulk solids get into sticky situations all the time — it’s just part of the business we’re in. Everything from the temperatures in your plant to your rotary valve configuration can affect the flow of material, for better or worse.
Problems with flow lead to blockage in bins, hoppers and silos. ACS Valves recently exhibited at the Advanced Design and Manufacturing Expo (ADM) in Toronto, where we heard Tracy Holmes, President of Jenike & Johanson, discuss the issue in more detail.
Here are some takeaways from her presentation.
When flow problems pile up
What starts with a small amount of buildup can quickly turn into a more serious problem. Poor flow leads to issues like reduced capacity, inconsistent flow, vibrating equipment, caking material and jamming.
Holmes says operators commonly make the mistake of treating their powders and bulk solids like liquids. Unlike liquids, bulk solids are collections of particles and won’t take the shape of a container in the same way.
“If you’re designing a system to handle liquids, you look for certain properties, like density or viscosity,” she explains. “Bulk solids are not the same. There are key values you need to know to design a system properly.”
Some of these values include pressures, wall friction, bulk density, permeability and cohesive strength.
Two common flow issues
Holmes described two flow issues that commonly occur in bins, hoppers and silos: arching and ratholing.
When bulk solids build up into an arch or dome-like shape over the hopper’s outlet and block the flow, it’s called arching or bridging. Arches come in two types: interlocking arches, built up of large, mechanically interlocked particles; and cohesive arches, which form when particles bond together from conditions like moisture, particle shape or temperature.
“It’s like several people trying to get through a door at the same time,” Holmes says.
Ratholing creates stronger structures that are more difficult to break. Ratholes shaped like cylinders form when discharge is restricted to a flow channel above the outlet. If you’re working with cohesive material, it may cake up outside the channel instead of flowing through.
Either issue can eventually lead to a jam or stopped flow.
Hopper discharge patterns
According to Holmes, the right discharge pattern in your bin, hopper or silo can prevent flow issues and their corresponding symptoms.
A funnel flow pattern, where some material moves while the rest stands still, means the silo walls lack the steepness and friction to promote consistent flow. It creates many of the problems mentioned above, from caking to ratholing.
Mass flow prevents ratholes. It promotes uniform flow with steeper, smoother walls and an outlet diameter large enough to allow the discharge rate you need.
Lastly, when you place a mass flow hopper under a funnel flow hopper, you get expanded flow. That creates a large enough flow channel to destabilize ratholes.
How flow can you go?
To prevent flow issues, it’s important to understand the material’s flow properties and design your conveying system accordingly. Your choice of rotary valve will have a significant impact on the overall flow rate.
ACS Valves can recommend a valve that makes sense for your material, your facility and the rest of your system. Get in touch to find your custom configuration.