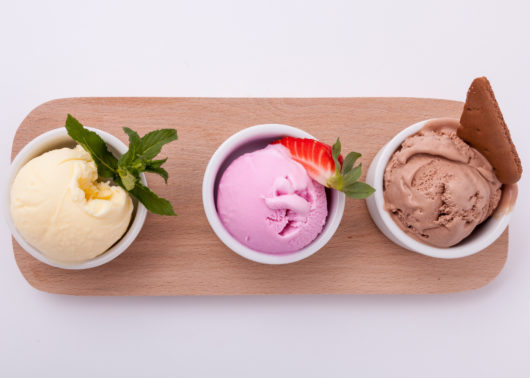
Some choices are easy. Chocolate or vanilla? A new Netflix series or a Seinfeld rerun? A Quick-Clean rotary airlock valve for fast disassembly, or a CI-XTR series with a food-grade anti-corrosion coating?
That last choice is not so simple, but it’s one where ACS Valves can help. To help you understand your options, we previously talked about three important things to consider when you’re selecting a rotary valve.
Let’s look at three more.
1) Energy efficiency
Different types of rotary valves and options may impact energy efficiency, but one key factor is the type of motor used. Direct drive packages do away with the added friction of a chain, providing higher torque at a lower RPM.
Another option is a variable frequency drive or variable speed drive (BFD/BSD), which lets you turn a dial to increase or decrease speed. That puts the power in your hands to optimize power and material flow as production levels change.
Are you planning to convey two similar products through one conveying line? A plug-type diverter valve, such as our Channel-Changer, lets you switch between two channels inside the valve housing. That’s one way to save energy by simplifying your equipment setup.
2) NFPA safety
If your material is considered a combustible dust, you must make efforts to comply with NFPA regulations. That applies to your rotary valves, too. Valves should be specifically designed to minimize the risk of explosions and fires in your plant.
An NFPA compliant rotary valve has a rotor with 8 vanes at minimum, a 3mm thickness and metal tips. It also has outboard bearings (not inboard), because these prevent combustible dust from accumulating. When it comes to shaft seals, we recommend ACST-4, which come with three quad rings over a Teflon® sleeve for the best possible seal.
At ACS Valves, all rotary airlock valves are NFPA compliant as a standard. It’s not something we consider an add-on feature. That said, we can provide tips on how to increase safety and regulatory compliance in your facility — all you have to do is ask!
3) Maintenance cycles
Maintenance requirements for a rotary valve vary depending on your material type. If your product is abrasive, corrosive, or prone to buildup, it may accelerate wear-and-tear on your valve and demand additional maintenance.
That’s where your rotary valve design comes in. For example, some valves come standard with coatings that resist corrosion and prevent sticky products from accumulating on surfaces. Others can be coated to resist abrasion from harder, more rugged materials.
When it comes to food-grade materials, a valve built on rails can drastically speed up the process of cleaning, maintenance and checking tolerances. Other types are designed to optimize air flow, so material doesn’t have a chance to stick in the first place.
In all cases, your choice can have a significant effect on the valve’s lifespan, efficiency and maintenance requirements.
Bonus tip: Manufacturing process
Do you know how your valves are manufactured? It’s important to look for housings that are properly cast and CNC-machined to provide smooth, durable surfaces and precise tolerances. Less reliable vendors may cast equipment that is pitted with cracks and crevasses where material can get stuck.
At ACS Valves, all of our products go through a strict inspection process to ensure the highest possible quality.
Ask a rotary valve expert
When the time comes to choose a new valve, you won’t have to do it alone. The staff at ACS Valves know conveying systems from top to bottom, meaning we can recommend something that fits your process perfectly.
Ready to meet a valve expert who speaks your language? Give us a call.