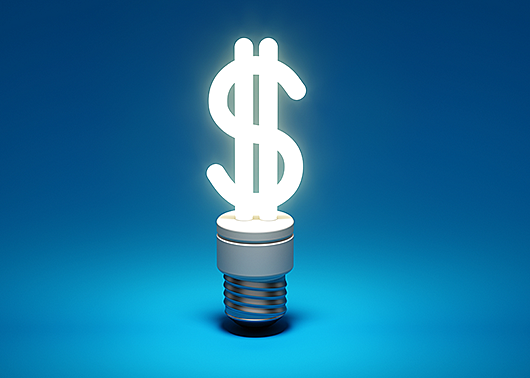
Coffee breaks are a great way to give employees an energy boost, but when it comes to your production process, are you using energy efficiently?
We all know the benefits of energy efficiency: besides keeping production costs low, it can contribute to a more sustainable manufacturing industry and promote a greener image for your brand.
Unless you convey coffee beans, we can’t recommend a strong cup of joe for your processing equipment. To keep energy use at a minimum, consider this advice instead.
1) Perform regular energy audits
You might associate audits with having to spend money on upgrades, but they can also identify changes you can implement quickly and cost-effectively. Besides, a primary goal of an energy audit is to identify ways to save you money long-term.
The audit can help you discover the main drivers of energy consumption and how much energy they use up in your process. It can also uncover opportunities to save energy, plan out your next steps, and calculate how much money you can save as a result.
If you choose to do the audit yourself, some government bodies provide guidebooks, checklists, and resources to guide you through it. Otherwise, you can always find an energy specialist to help you.
2) Schedule production around peak hours
Operating all your machinery during peak energy hours can lead to a big chunk of extra charges on your monthly utility bill. To mitigate this, you can strategically schedule energy use by staggering production startups and shutdowns. Consider which machinery uses the most energy and schedule it during off-hours.
Talk to your utility vendors to come up with the best schedule for your plant. They may also be able to review your current energy use and offer incentives to improve it.
3) Make some upgrades
Some energy-saving solutions will be more involved than others, but they can be as simple as updating your plant’s insulation and windows. You could also consider investing in more energy-efficient equipment and tools, installing sources of renewable energy, or using smart manufacturing software to diagnose and optimize areas of high energy consumption.
With all the options out there, it might be more helpful to start with that energy audit to determine what would make the most sense for your facility. You should also check for any government incentives that might help you upgrade machinery and equipment to more energy-efficient models.
4) Maintain your machinery
Equipment maintenance plays a big role in the overall energy efficiency of your plant. Put simply, you risk wasting energy when equipment isn’t performing at its best.
In the case of rotary airlock valves, you should replace the rotor whenever the clearances get too big. Even the best airlocks need this critical piece of maintenance to avoid material leakage and keep flow at maximum efficiency.
5) Use variable speed drives
Traditional motors run at fixed speeds, which results in a constant rate of energy consumption regardless of the workload. Variable speed drives, also called variable frequency drives (VSD/VFDs), help save energy by allowing motors to operate at varying speeds depending on the current load.
VSDs are available for a range of equipment types. In rotary airlocks, you can install one to increase or decrease the speed at the turn of a dial. That helps you avoid peak demand charges and optimize energy and material flow. You can also use VSDs to regenerate power and reroute it back into your system or sell it back to your utilities.
6) Choose the right motors for your airlock
Many rotary airlocks are built with chain drives, which adds friction from the chain and runs less efficiently as a result. Consider switching to a direct drive package. Because they don’t have to deal with chain friction, direct drives offer higher torque at lower rotations per minute (rpm).
They can also be equipped with a VSD for those extra energy savings we mentioned.
7) Get futuristic
If you’re looking to implement more tech or take a more innovative approach to energy efficiency, the industry has made plenty of strides in recent years.
One option is having a circular thermal or heat recovery system. This helps you recapture a percentage of waste heat that would normally get lost through stacks, cooling towers, and sewage, and harness that to supply a sustainable source of power to your plant.
You could also look into predictive maintenance software to help identify equipment issues before they happen.
Find the right partners
It always helps to partner with vendors who can support your sustainable initiatives. Contact ACS Valves to configure a rotary airlock that’s tailored to deliver maximum efficiency in your unique processing environment.