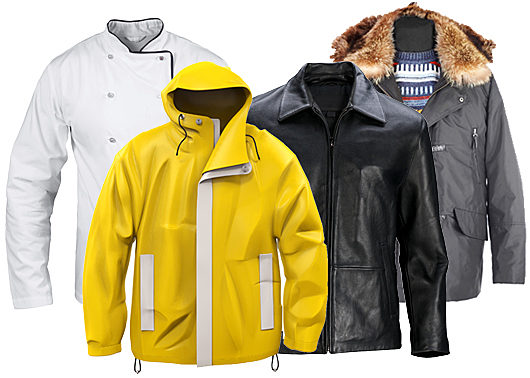
Though sometimes treated like an afterthought, coatings are an important feature in your rotary valve.
Choosing the right coating can significantly improve the performance and lifespan of your valve. Likewise, choosing the wrong coating—or opting out of a coating altogether[1]—can do the opposite for your productivity.
This is especially true for heavy-duty applications. Without coatings, abrasive materials wear on the rotor and affect the clearances where the rotor tip meets the housing. When that happens, it compromises the airlock seal, which causes leakage and general inefficiencies. This degree of wear often leads to shutdowns, lost productivity, increased maintenance and eventually equipment replacement.
For non-heavy-duty applications, such as processing sticky materials, coatings offer benefits that are just as important. Here, coatings improve cleanability for less downtime. They also improve material release for longer runtimes and less build-up—which would otherwise reduce capacity, jeopardize quality, or, if not dealt with, cause contamination. Where corrosion is a possibility, coatings protect the equipment from chemical attacks, and prolong the valve’s lifecycle.
Benefits of the right valve coating
- Improves material release
- Reduces rotor replacements
- Improves cleanability of the valve
- Minimizes downtime and maintenance
- Prevents build-up of sticky materials that can cause quality issues or even contamination
- Prevents capacity reduction
- Prevents corrosion or chemical attacks
- Prolongs the life of valve (by about 3x)
- Resists wear and abrasion
- Prevents material leakage
Tungsten. Chrome. Teflon®. Stainless. Which coating to choose?
That depends. Are you processing aggregate or polyamides? Sugar or pet food?
What we’re trying to say is it’s worthwhile to ask!
We have a lot of knowledge around this topic. In fact—just like every other detail of your rotary valve—every coating solution is custom-designed, manufactured, and installed to meet the demands of your application.
We match the alloy characteristics with your specific process, factoring in material(s), conveying system, operating temperature, and performance goals. We also make recommendations on coating thickness and where the coatings should be applied on the valve interior (e.g. rotors, endplates, housings, etc.).
Talk to us about the right coating for your valve.
[1] This, of course, depends on your application. There are some processes for which coatings are unnecessary—they just aren’t in the majority.