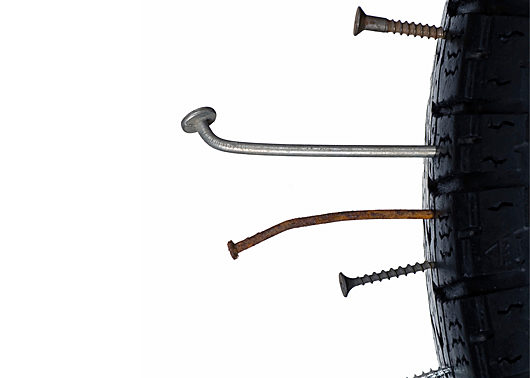
Rotary airlocks are designed to keep a consistent pressure differential, so material can travel efficiently through the pneumatic system. They do this by “locking” or sealing the airflow between the inlet and outlet. Without airlocks, pressurized air would be to flow upwards, block material from entering the inlet, and reduce flow drastically.
Having said that, ‘airlock’ is a misnomer, because even the best ones will leak.
In fact, it’s not only normal for small amounts of air (also called blow-by) to travel back up through the rotor, leakage is something valve manufacturers account for when we recommend the valve.
Leakage can be minimized—which is why we emphasize the importance of getting the right airlock—but it cannot be eliminated.
Why do airlocks leak?
By design, airlocks are not perfect air seals. They can’t be. Here’s why:
- For proper operation, rotor blades cannot come into contact with the housings. There must be a clearance between them. Clearances are very small—measured in thousandths of an inch—but they are there nonetheless, and air can escape through them.
Clearances are determined by accounting for all modes of operation, taking into consideration speed; high temperatures (and unequal thermal expansion of the rotor and housing); displacement of the housing under the material load; rotor runout; etc.
- When material enters the rotor pockets, it displaces gas. Some gas leaks out of the clearances, and some of it—when exposed to pressure at the outlet—remains sealed within the rotor until it comes around to the inlet, where it is released into the feed hopper and impedes material flow.
The total amount of rotor displacement leakage is determined by pressure differential across the valve, rotor pocket volume, product feed rate, and valve shaft speed.
How to minimize leakage?
Before you order the valve, be sure to talk to your supplier about the specific material conveyed, your production goals, pressure rates and your existing equipment.
Leakage can be predicted with a simple calculation, so consulting with your supplier at the design phase will allow them to factor in your details and determine the right airlock style, rotor features, rotor speed and size.
Once you have the right valve, replace your rotor when necessary to maintain tight clearances. Even the best abrasion-resistant equipment will wear over time, which can increase the clearance between the housing and rotor.
Finally, since we know you can’t eliminate leakage, it is imperative to capture and redirect the air that is in your system through proper venting. Venting can be done directly from the body of the airlock—if equipped with the right connection—or from a small, vented transition hopper that can be installed between the feed source and the airlock. Your supplier will be able to recommend the right venting system for your application.