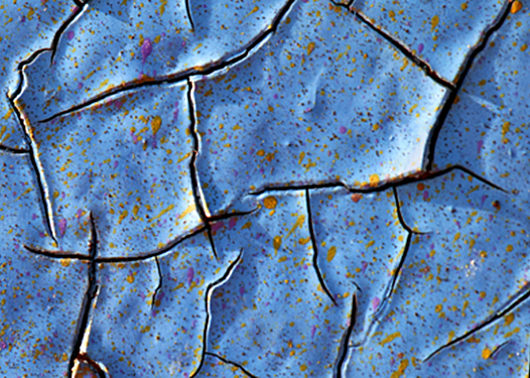
You’ve done everything right.
Your mixture of blues and yellows have cooperated well and achieved a shade of green that even the amazon jungle would envy.
But before you get the chance to add your resin, solvents and other additives, you notice…your green is looking a little brown.
It’s almost as though your machinery wanted to join your awesome green party, dropping bits of corroded metal into the mix, instead of realizing that it was never invited.
So how do you keep your machinery from and corroding, or causing unwanted cross-contamination in your end product?
Let’s break it down, so your machinery doesn’t:
Apply coatings to extend your equipment’s life
There are a number of benefits that coatings can add to your machinery. Their main function is to prevent imperfections and surface cavities caused by material wear.
If there are any cracks or imperfections in the rotor, you could end up with material build-up which, with certain materials, could lead to corrosion or chemical attacks over time. Because of this, coatings will also extend the life of your machinery, and improve material flow.
What should your machinery be made of?
Stainless steel is usually the standard for rotary valves in the chemical industry. Some chemicals cause mass material wear on cast iron construction valves. As a result, these valves are more likely to corrode and damage your end product.
Keep your equipment clean and compliant
There are certain features that you can have manufactured into your rotary valves to make cleaning a lot easier for your people on the plant floor. We stand by our U-Shaped rotor pockets as a great way to prevent material build up and improve flow.
Imagine your paint pigments getting stuck at the bottom of your valve. Pigments will end up mixing and damaging your end product.
It’s also a good idea to switch out your chain drive packages to direct drive packages. Chain drives require constant maintenance and lubrication that has the potential to contaminate your end product.
ACS has engineered features into our valves such as the QuickClean RotorRail™ that allows for tool-less access into the rotor so that cleaning can be finished in a manner of minutes.
You can also prevent the cleanup and contamination risk that comes from bearing seal leaks by replacing them with glandless shaft seals.
Keep your plant workers safe from potentially dangerous cross-contamination
It’s integral that you provide Material Safety Data Sheets (MSDS) to your plant workers who are directly dealing with valve maintenance that are conveying potentially hazardous materials.
This will help them identify how to handle cleaning the materials, whether their cleaning materials can react with your product, and what to do if accidents occur. It can also help recognize symptoms of overexposure.
The consequences of handling your materials improperly can not only ruin your end product, but also has the potential to lead to fires or explosions depending on the combustibility of your material, putting your plant workers in danger. This can be further mitigated by ensuring your plan is properly ventilated.
This should go without saying, but always provide your workers with proper respiratory protection, safety glasses and other protective clothing as mandated by the OSHA.