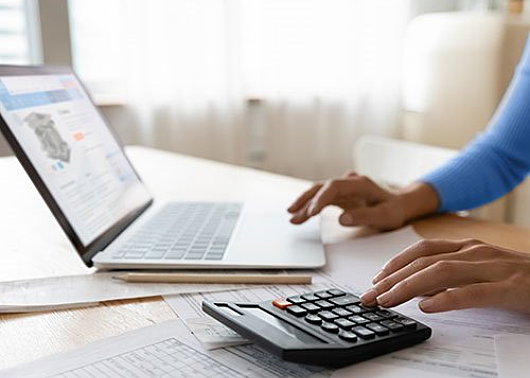
In this article:
- What do I get for the price of a rotary valve?
- Why would I need to customize it?
- What information do you need to quote a valve?
- What goes into my quote?
- Can I get my quote quickly?
- So, how do I get started?
Here’s a quote for you: “It’s so much easier to suggest solutions when you don’t know too much about the problem.” (Malcolm Forbes)
That’s probably not the kind of quote you were wondering about, but it speaks to something we see a lot in the material processing industry. As a processor, you’re an expert in your application, and it only makes sense to work with a supplier who knows just as much about your industry.
That’s how we approach quotes here at ACS Valves. With a combined 40 years of experience working with rotary airlock valves and conveying systems, our team can recommend the solutions you really need – not the ones that will inflate your budget.
It’s not an easy thing to do, but it’s something we take pride in.
Now that you know that about us, here’s an overview of the quotation process at ACS Valves.
What do I get for the price of a rotary valve?
If there’s one thing we can guarantee, it’s the overall quality of construction. Because they’re cast in North America, our valves have superior metallurgy compared to something you might find overseas. That means the steel is strong and smooth, with no cracks or crevasses for material to build up.
Our rotary valves also have a more durable shaft seal type and more efficient motors.
Then there’s configuration. Remember all those decades of experience we mentioned? Our team uses that to size and customize valves that perfectly fit your application.
Why would I need to customize it?
None of our valves are sold off-the-shelf. We see customized valves as a necessity, not a luxury, because each application has its own differences and quirks.
Typical customization options include coatings, rotors, and accessories. One option might prevent a sticky substance from clogging up the system, while another might protect the valve from abrasion.
When they’re configured properly for your application, rotary valves experience less build-up and leakage, require less maintenance, and last longer.
We try our best to understand each industry to provide economical valve choices that will give you the best value for your dollar.
What information do you need to quote a valve?
The more information you can give us, the better. To size a valve, we need to know the material, bulk density, and capacity. Knowing the material (your ingredient) helps us determine the valve’s materials of construction and coatings (if any), while application details let us know if you need features like a vent port or high-temperature design.
Here is a quick look at what we ask for on a typical request form:
- Will the valve act as an airlock, feeder, or combination?
- What piece of equipment sits above the rotary valve?
- What equipment sits below the valve?
- What are your material characteristics (things like bulk density, shape, and abrasiveness)?
- What are your NFPA requirements?
- What is the flow rate?
What goes into my quote?
The quotation document includes details like the materials of construction, coating, rotor type, NFPA compliance features, motor details, added accessories – and prices, of course.
We may also provide a recommended option that you can add to improve the valve’s reliability, efficiency, and longevity. Finally, you’ll find the purchase terms and a timeframe for delivery.
Along with the quote, we’ll attach any spec sheets, pictures, 3D models, or paperwork you might need.
Can I get my quote quickly?
In most cases, we have a 24-hour turnaround from request to quote. If we have a sales rep in your area, we can send someone down to your facility to see the system firsthand for a more accurate quote.
If you have a repeat order, find the sticker on your rotary valve and give us the serial number. We can pull up your existing file and, if nothing has changed, we’ll send you the same order as before.
So, how do I get started?
There are lots of ways to get a quote. The most common is to give us a call (905-765-2004) or send us an email (sales@acsvalves.com), but you can also start the process by using our contact form, trying our Rotary Valve Sizing Tool to get a quick glance at the valve you’ll need, or chatting with the chatbot on our website (who is actually a live rep between the hours of 9-5).
The ACS Valves sales team is supported by an exceptional technical staff, so we can answer any question you throw our way. We look forward to hearing from you!