
What is deflagration?
Deflagration is a form of combustion that occurs when a heat source moves over and ignites cold materials (i.e. combustible dusts), creating a very fast moving fire.
Deflagration fires are very unpredictable forms of combustion because they move so quickly. It is sometimes difficult for fire crews to put out as hot materials could continue to combust.
A deflagration fire could continue to spread along your line, sometimes destroying entire manufacturing plants and endangering the lives of workers.
How does deflagration happen in your machinery?
There are three elements needed for a fire in your plant.
- Fuel
- Oxidizer
- Ignition source
The fuel, in this scenario, would be your combustible dust.
The oxidizer would be a high concentration of oxygen that could result from leaks in your system or improper ventilation somewhere within the system.
Ignition can be created from friction or elevated material temperatures in your conveying line. This could be caused by material drag or build up, axial shaft movements or increased rotor speeds. In a positive-pressure conveying system, air entering the system could become elevated as a result of being compressed.
There are two other additional elements that are needed to turn your fire into a combustible dust explosion:
- Concentration of dust particles
- Confinement of dust
These two final elements can be categorized as dust clouds. They can collect both inside and outside of your machinery by resting on surfaces or in the air. These dust clouds pose high risks when mixed with high levels of oxygen.
Together, the five elements create what is known as an explosion pentagon, as shown in the image below.
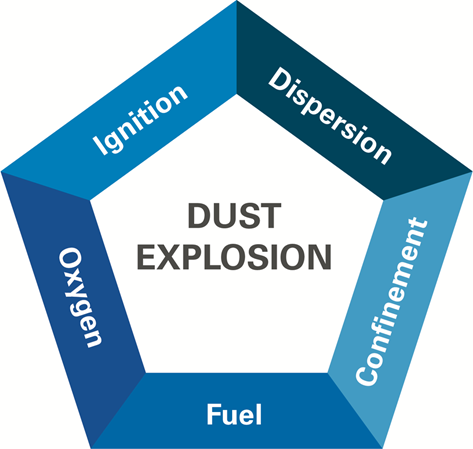
How can you prevent deflagration in your plant?
If one or more of the elements in the explosion pentagon are missing from your system, then you should successfully be able to prevent a dust explosion and resulting deflagration.
Plant and worker safety is important to ACS, which is why we continue to manufacture NFPA compliant valves.
The NFPA guidelines for codes 68 (Explosion Protecting by Deflagration Venting), 69 (Standard on Explosion Prevention Systems, and 8503 (Standard for Pulverized Fuel Systems) outline ways to mitigate or control these risks.
For example, to prevent your materials from heating up as they enter your system due to the compression of gas or air, install an air cooler along the line before your material feeder.
Sizing your rotary airlocks properly can also help with material flow, and ultimately reduce combustible build up along your line. You should also have a proper ventilation system for your application to ensure that products are flowing in the right direction, and not leaking or travelling from your valve back up into the hopper.
If you would like to learn more about NFPA compliant valves, and how to control or prevent deflagration in your plant, talk to an ACS rep today.