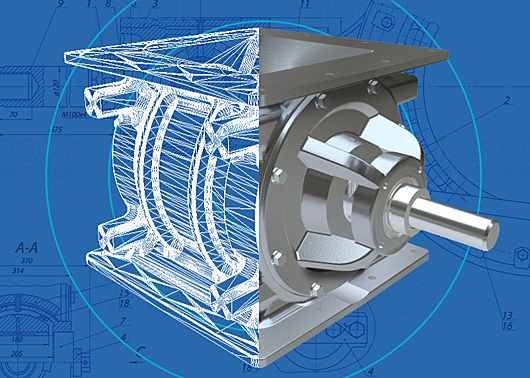
As we look forward to 2019 and all the new manufacturing tech developments that come with it, the engineers at ACS have our own technological trend prediction for the new year. We think 3D product rendering will make a big splash in the manufacturing world — and here’s why.
It’s much easier to visualize products.
With our own transition from 2D to 3D drawings well underway, ACS has updated virtually all imagery of the valves, accessories and other equipment on our website. Visitors can now click, rotate and zoom in on 3D models to get a much better understanding of products compared to static 2D images.
Your average 2D image is limited to one angle and prevents the viewer from seeing important details. When customers view a product in 3D, they can better understand its form, function and operation, as well as its overall size and proportions, which makes it easier to understand how the product will fit their applications and plant layout.
To make things even easier, we also deliver 3D solids of our products for customers who want to drop them into floor plans.
It improves product designs.
3D isn’t just for customers or suppliers, though — it also helps manufacturers design and build better products. For example, ACS’ virtual models allow for enhanced visualization, interference checking, stress and strain analysis, weight calculation and better drawings for our shop.
This all translates into better designs, as well as faster and more accurate revisions and improvements on existing designs. For example, if the customer requested a change in the height of a spool-style shear protector in 2D, we would have to meticulously revise several drawing views in addition to separate laser cut drawings used in the parts manufacture.
The same change with a 3D model could be as simple as changing a single numerical value. The rest is automatic as the 3D software will update all components affected by the change in height. Then, with a few more key strokes, all the shop drawings and laser cut drawings can be automatically updated as well.
This turns an hour-long job into a 10-minute job. It also eliminates numerous operations that could introduce human error and makes it easier to evaluate the end result to see if the revision is satisfactory.
Manufacturers can also use virtual product models to create plastic molds, 3D printed components (additive manufacturing) or input data for CNC machines.
Simply put, 3D designs improve quality, reduce design costs and get your products to market more quickly.
You can see special features in action.
Depending on how detailed you want to get with your 3D model, you can also use it to show off a product’s special features — like the ACS Quick-Clean RotorRail™ and its tool-less access point.
Animations let your customers see these special features in action, which helps them visualize how to operate the product. An exploded view also comes in handy when you need to show the product’s assembly and components.
It helps educate customers and operators.
3D modeling is a great educational tool for our customers. It adds a more immersive experience to training, technical documents, and instruction in product operation and maintenance, giving staff a 360 view of products — the next best thing to a hands-on experience.
To give you another example (with animations and all), see our video guide to removing the drive side endplate on an ACST-4 seal.
Ready to see it in 3D?
Our engineers are excited to keep developing models and 3D visualizations of our products. For more examples and an up-close-and-personal look at our valves, check out the 3D gallery.